A5056合金の加工性と機械的特性の解説
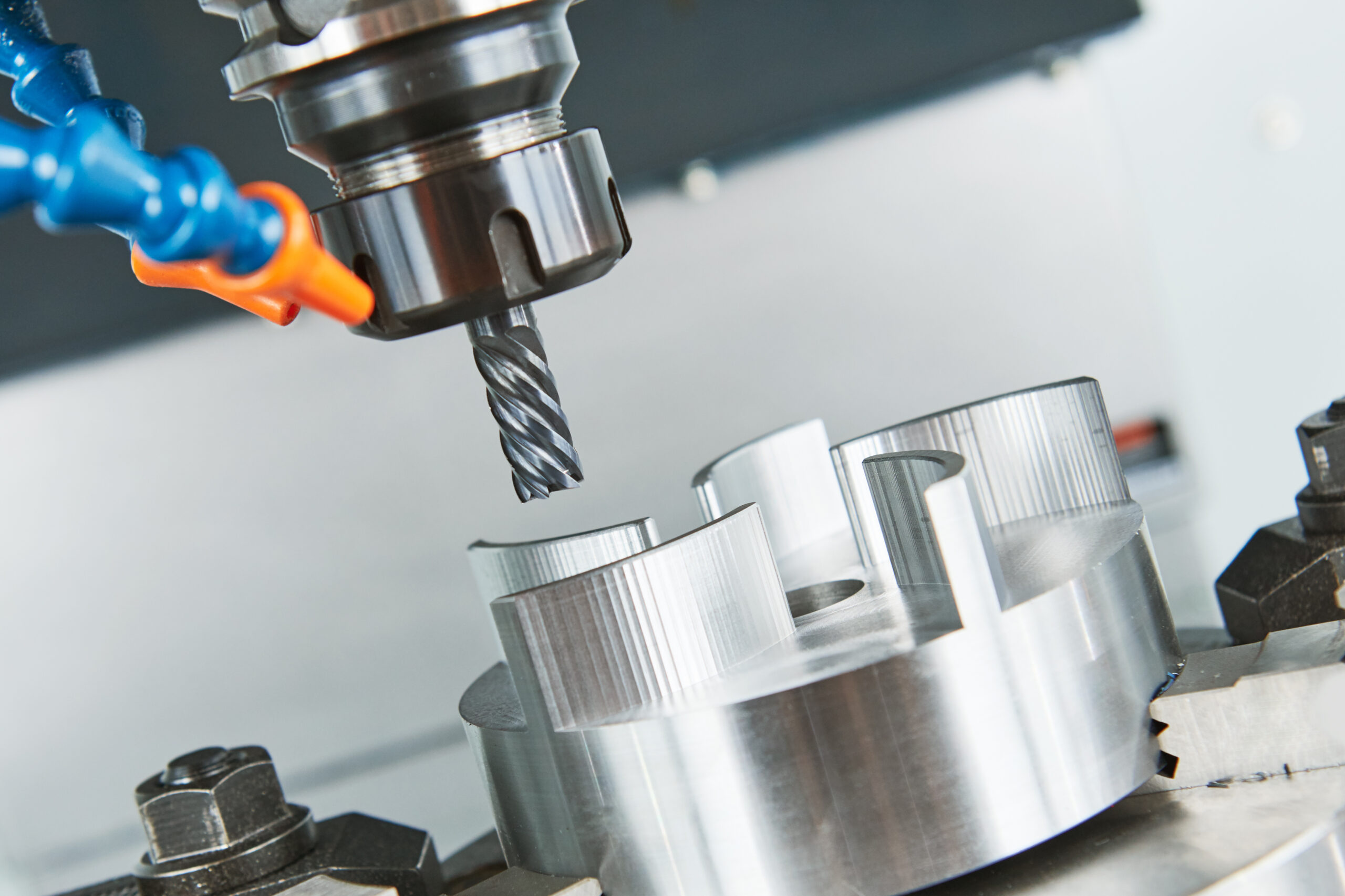
A5056合金は、様々な産業で広く使用されている素材であり、その加工性や機械的特性は重要なポイントです。本記事では、A5056合金の加工性と機械的特性について詳しく解説します。この合金の特性を理解することは、製品開発や加工工程において大きな影響を与えることができます。特に、ヤング率はこの合金の特徴の一つであり、その影響についても詳細に説明します。A5056合金に関心がある方やこの素材を使用している方々にとって、貴重な知識を提供することを目指しています。加工性や機械的特性についての理解を深めることで、より効果的な活用が可能となります。
目次
A5056合金とは
A5056合金は、アルミニウムを主成分とするマグネシウム系合金の一種であり、優れた耐食性と中程度の強度を持つことが特徴です。主に軽量性と耐久性が求められる分野で使用されています。A5056合金の成分と一般的な用途
成分 | 含有量 (%) |
---|---|
アルミニウム (Al) | 約95.0~97.0 |
マグネシウム (Mg) | 約4.5~5.6 |
マンガン (Mn) | 約0.05~0.2 |
クロム (Cr) | 約0.05~0.2 |
鉄 (Fe) | 最大0.4 |
シリコン (Si) | 最大0.3 |
一般的な用途
A5056合金は、以下のような用途に利用されます:- 船舶・海洋構造物:優れた耐食性により、海水環境下での使用に適しています。
- 自動車部品:軽量で強度が求められるホイールやフレーム部品に使用。
- 航空宇宙分野:強度と耐久性を活かし、構造材や装備品に使用。
- 電気・電子機器:軽量で加工しやすいため、各種部品に適用。
- 建築材料:耐久性を活かし、外装パネルや構造材に利用。
A5056合金の市場での位置付け
A5056合金は、マグネシウム含有量が高いアルミニウム合金の中でも耐食性と強度のバランスが取れた素材として市場で評価されています。市場での特徴
- 耐食性の高さ:特に海水や塩害環境下での使用に適し、海洋産業での需要が高い。
- 加工性の良さ:塑性加工性が優れ、板材や押出材として多く使用される。
- コストパフォーマンス:高強度アルミ合金(A7075など)より低コストであり、広範な用途に適用可能。
- 競合材料との比較:
- A5052との違い:A5056はマグネシウム含有量が高く、より高い耐食性を持つが、若干の強度低下がある。
- A6061との違い:A5056は耐食性に優れるが、A6061の方が強度は高い。
A5056合金の特性
物理的特性
A5056合金は、密度が約2.66 g/cm³と軽量でありながら、耐食性に優れるアルミニウム合金の一種である。融点は約595~650℃で、中程度の耐熱性を持つ。熱伝導率は約121 W/m·Kと比較的高く、放熱性が求められる用途にも適している。また、電気伝導率は約28-32 %IACSであり、アルミニウムとしては標準的な値を示す。線膨張係数は24.5×10⁻⁶ /Kで、温度変化に対する寸法安定性も一定の水準を保っている。化学的特性
A5056合金はアルミニウムを主成分とし、4.5~5.6%のマグネシウムを含むことで耐食性を向上させている。マンガンやクロムを微量添加することで、合金全体の強度と耐摩耗性を高めている。鉄とシリコンの含有量は最大0.4%および0.3%と低く抑えられており、機械加工性や溶接性に悪影響を与えないよう設計されている。この組成により、A5056は特に海水環境下での耐久性が求められる用途に適している。A5056のヤング率とは
A5056合金のヤング率は約70 GPaであり、アルミニウム合金としては中程度の剛性を示す。この特性により、衝撃荷重に対する耐久性がありながらも、適度な柔軟性を持つ。降伏強さは約180 MPa、引張強さは約250 MPa、伸びは約12~15%とされており、機械的特性のバランスが良いことが特徴である。加工性の高さから、航空機、船舶、電子機器、自動車部品など多様な分野で利用されている。A5056合金の機械的特性
引張強度と硬さ
A5056合金の引張強度は約250 MPa、降伏強度は約180 MPaとされており、アルミニウム合金の中でも比較的高い強度を持つ。硬さ(ビッカース硬さ)は約75~85 HVであり、一般的な加工用途に適した硬度を示す。冷間加工や圧延加工によって硬さが向上するため、用途に応じた調整が可能である。疲労強度と耐食性
A5056合金は、繰り返し荷重を受ける環境下でも比較的安定した疲労強度を持つが、過度の応力集中が発生すると亀裂が生じやすい。そのため、設計時には応力分散を考慮する必要がある。一方、耐食性に関してはマグネシウムを含むことで優れており、特に海水や塩害環境での使用に適している。アルマイト処理を施すことで、さらに耐食性を向上させることが可能である。A5056合金のヤング率による影響
A5056合金のヤング率は約70 GPaで、適度な剛性と柔軟性を併せ持つ。この特性により、振動や衝撃荷重を受けた際の変形を適度に吸収し、構造体の安定性を保つことができる。そのため、航空機、船舶、自動車部品などの分野で利用されている。また、適度な剛性を活かして、電子機器の筐体や軽量構造材としても広く採用されている。アルミニウムA5056の加工性
切削加工
A5056合金は比較的良好な切削性を持ち、汎用的な工具での加工が可能である。ただし、アルミニウム特有の粘りがあるため、切削時に刃先へ溶着(ビルトアップエッジ)が発生しやすい。このため、以下の工夫が必要となる。- 工具材質:超硬やダイヤモンドコーティング工具を使用すると溶着を抑えられる。
- 切削速度:高めの切削速度を設定し、適切な送り速度を維持する。
- 切削液:油性や水溶性の切削液を使用し、熱を分散させることで工具寿命を延ばす。
曲げ加工とその他の成形方法
A5056はマグネシウムを含むため強度が高く、他のアルミ合金と比較してやや成形性に劣る。ただし、適切な条件を設定すれば問題なく曲げ加工が可能である。- 曲げ加工:
- 曲げ半径は板厚の2~3倍以上を確保すると割れを防げる。
- 曲げ方向は圧延方向と直角にすると良好な結果が得られる。
- 焼鈍(アニーリング)を行うことで加工性が向上する。
- その他の成形方法:
- プレス加工:適度な塑性変形が可能だが、高強度のため金型に負荷がかかりやすい。
- 溶接:TIGやMIG溶接に適しているが、溶接部の強度低下に注意が必要。
- 押し出し加工:良好な押し出し特性を持ち、複雑な断面形状の製品が製造可能。
加工時の注意点と工夫
A5056の加工時には、強度や耐食性を維持しつつ、加工精度を確保するために以下の点に注意する。- 熱の影響:
- 切削加工や溶接時に熱が加わると、局所的に硬度が低下しやすい。
- 加工後の熱処理を適用することで機械的特性を維持できる。
- 表面処理:
- アルマイト処理を施すことで耐食性が向上する。
- 精密部品の場合、加工後の仕上げ研磨が必要になる場合がある。
- 工具摩耗:
- A5056はアルミ合金の中でもやや硬めの部類に入るため、工具の摩耗が進みやすい。
- 高性能コーティング工具を選定し、適切な切削条件を設定することで工具寿命を延ばせる。
A5056合金の選定と取り扱い
合金選定のポイント
A5056合金は、アルミニウム-マグネシウム系合金の一種であり、耐食性や強度に優れるため、特定の用途に適している。選定時には以下の点を考慮する。- 耐食性の必要性
- A5056は海水や湿気の多い環境に強いため、船舶や海洋構造物に適している。
- 他のアルミニウム合金と比較して耐食性が高く、特に塩害に強い。
- 強度と成形性のバランス
- A5056は中程度の強度を持ち、プレス加工や切削加工に適している。
- 高強度が求められる場合はA5052、さらなる耐食性が必要な場合はA5083が選択肢となる。
- 溶接適性
- TIG・MIG溶接が可能であり、溶接構造物の材料として使用されることが多い。
- 溶接時の強度低下を考慮し、補強設計が必要な場合がある。
- 用途に応じたコストパフォーマンス
- A5056は比較的コストパフォーマンスが良く、航空機部品、建築材、自動車部品などの大量生産用途に適している。
保管と取り扱いのベストプラクティス
A5056合金を適切に保管・取り扱うことで、品質を維持し、加工時のトラブルを防ぐことができる。- 保管方法
- 湿気を避け、乾燥した環境で保管する。
- 直射日光の当たらない温度変化の少ない場所に保管する。
- 板材や棒材は平置きではなく、立てかけるか専用ラックを使用する。
- 酸化防止対策
- 長期間保管する場合、酸化を防ぐために防錆油やラッピングフィルムで保護する。
- アルマイト処理を施すことで表面の酸化を防げる。
- 取り扱い時の注意点
- 表面に傷がつきやすいため、ゴム製手袋や布製の保護材を使用する。
- 重量物の場合、フォークリフトやクレーンを用いて安全に移動させる。
- 切削や溶接時の粉じん対策として、換気設備を整え、適切な作業環境を確保する。
A5056合金の溶接性
溶接方法とその特徴
A5056合金は、アルミニウム-マグネシウム系合金であり、一般的な溶接方法に適応するが、適切な方法を選択することが重要である。- TIG溶接(タングステン不活性ガス溶接)
- 高品質な仕上がりが可能で、薄板や精密な部品の溶接に適している。
- 溶接熱によるひずみが少なく、比較的安定した溶接ができる。
- 低速なため、作業効率はやや低い。
- MIG溶接(金属不活性ガス溶接)
- 高速での溶接が可能で、大型部品や厚板の溶接に適している。
- 溶接ビードが比較的太く、溶接後の仕上げが必要になる場合がある。
- 作業効率が高く、大量生産向けの用途に適している。
- レーザー溶接
- 高精度で熱影響が少なく、歪みを抑えられる。
- 低入熱での溶接が可能なため、熱変形が少ない。
- 設備コストが高く、大規模な生産ライン向けの技術となる。
溶接時の問題点と対策
A5056合金を溶接する際には、以下の問題が発生しやすい。- 溶接部の割れ(ホットクラック)
- アルミニウム合金は溶融状態での収縮が大きく、割れが発生しやすい。
- 対策
- 溶接前に十分な予熱を行い、熱影響を均一にする。
- 低温割れを防ぐために、適切な溶接速度と溶加材を選定する(推奨される溶加材:5356系または5183系)。
- 気孔の発生
- アルミニウムは水素を吸収しやすく、溶接中に気孔が発生しやすい。
- 対策
- 溶接前に母材の表面を十分に清掃し、酸化皮膜や油分を除去する。
- 適切なシールドガス(アルゴンまたはアルゴン-ヘリウム混合ガス)を使用し、ガス供給を安定させる。
- 熱影響による強度低下
- A5056は熱による強度低下が起こりやすく、溶接部の機械的特性が低下することがある。
- 対策
- 溶接後に徐冷(ゆっくり冷やす)を行い、急激な冷却を避ける。
- 可能な場合は熱処理を施し、強度を回復させる。
A5056合金の熱処理
熱処理の目的と効果
A5056合金は、アルミニウム-マグネシウム系合金であり、特定の熱処理を施すことでその機械的特性を大きく改善することができます。熱処理の目的と効果は以下の通りです。- 目的
- 強度の向上:A5056合金の溶接後や加工後に、適切な熱処理を施すことで強度を回復させる。
- 耐食性の向上:熱処理を通じて、アルミニウム合金表面の耐食性を強化する。
- 加工性の改善:材料を均一にすることで、後の加工や成形が容易になる。
- 組織の均質化:熱処理により、金属内部の結晶構造や組織が均一化され、性能のばらつきが少なくなる。
- 効果
- 機械的特性の改善:硬度、引張強度、耐摩耗性が向上する。
- 残留応力の低減:加工や溶接後の残留応力を減らすことで、製品の変形やひずみを防ぐ。
- 寸法安定性の向上:熱処理後、部品の寸法精度が改善され、製品の安定性が向上する。
熱処理プロセスの種類
A5056合金に適用できる主な熱処理プロセスは以下の通りです。- 焼鈍(アニーリング)
- 焼鈍は、材料を高温に加熱した後、徐冷して内部のひずみや残留応力を取り除くプロセスです。
- 目的:加工後に残る内部応力を除去し、材料を均一にする。
- 効果:強度は一時的に低下するが、延性や加工性が改善され、後の加工が容易になる。
- 時効硬化(エイジング)
- 時効硬化は、A5056合金を高温で加熱し、その後、冷却して強度を向上させるプロセスです。
- 目的:アルミニウム合金の強度を高める。
- 効果:合金内での析出物が結晶化することにより、材料の硬度と引張強度が増加する。
- 時効硬化は、特にA5056合金においては強度向上に寄与しますが、過度の時効硬化を行うと延性が低下することがあります。
- 溶体化処理(ソリューション・テンプ)
- 溶体化処理は、高温で合金を加熱し、合金成分を均一に溶かしてから急冷するプロセスです。
- 目的:合金の構造を均一にして、次の時効硬化や冷却による結晶構造の変化を制御する。
- 効果:均一な溶解によって、結晶粒が小さくなり、合金の全体的な強度が向上します。
- 焼戻し
- 焼戻しは、焼鈍後に材料を再加熱して特定の特性を引き出す処理です。
- 目的:焼鈍後の素材の硬度や靭性を調整する。
- 効果:高い硬度や強度を持たせることができ、材料の適性を最適化できます。
A5056合金の表面処理
表面処理の種類と目的
A5056合金に対する表面処理は、耐食性、耐摩耗性、外観の向上、さらには機械的特性の改善を目的として行われます。主な表面処理の種類とその目的は以下の通りです。- アルマイト処理(陽極酸化)
- 目的:アルミニウム合金の表面に酸化皮膜を形成し、耐食性や硬度を向上させる。
- 効果:酸化皮膜は非常に硬く、耐摩耗性を高めるとともに、腐食に対する耐性を強化します。また、アルマイト処理によって表面に美しい光沢や色合いをつけることも可能です。
- メッキ(亜鉛メッキ、クロムメッキ)
- 目的:A5056合金の表面に金属メッキを施すことで、耐食性や装飾性を向上させる。
- 効果:亜鉛メッキは特に防錆効果が高く、クロムメッキは外観の美しさとともに耐摩耗性も向上させます。クロムメッキによる滑らかな表面が摩擦の低減に寄与する場合もあります。
- パーカー処理
- 目的:鉄や鋼に対して使用されるパーカー処理を、アルミニウム合金に適用することにより、耐食性を高める。
- 効果:酸化皮膜のように合金表面を保護し、さらに美観を向上させることができます。
- スプレー塗装
- 目的:合金表面を塗料で覆うことで、外的な環境からの保護を強化する。
- 効果:耐食性の向上、また、塗装色を自由に選択できるため、外観の美化が可能です。
- レーザー処理
- 目的:レーザーを用いて表面に微細な加工を施すことで、局所的な硬化や強度向上を実現する。
- 効果:局所的な耐摩耗性を高めることができ、特に動作部分などに有効です。
表面処理による性能向上
A5056合金の表面処理による性能向上は、以下のように期待されます。- 耐食性の向上
- 表面処理により、合金の表面が外部の環境から保護され、酸化や腐食から守られます。アルマイト処理やメッキ処理は特に優れた耐食性を発揮します。
- 耐摩耗性の向上
- 硬化した表面が摩擦による損傷を防ぎます。アルマイト処理やレーザー処理による表面硬化は、耐摩耗性を著しく向上させるため、動的な部品に有効です。
- 外観の改善
- 表面処理により美観が向上し、色調を選択できるため、製品のデザイン性が求められる場合に最適です。アルマイトやスプレー塗装による仕上げは、見た目の質感も向上させます。
- 摩擦の低減
- クロムメッキやスプレー塗装は、摩擦を減少させる役割を果たし、動作部品の効率を高めるとともに、摩耗を防ぎます。
A5056合金のトラブルシューティング
加工上の一般的な問題と解決策
A5056合金の加工中に発生する可能性がある一般的な問題とその解決策は以下の通りです。- 問題1: 切削時の表面品質の低下
- 原因:不適切な切削速度や工具の摩耗、または切削液の不足が原因となります。
- 解決策:切削速度の調整を行い、工具の種類と状態を見直すことが必要です。また、切削液の供給量や品質を確認し、適切な冷却を確保することで表面品質の向上が期待できます。
- 問題2: 加工中のひずみや歪み
- 原因:過度な切削圧や不均一な冷却が原因となることが多いです。
- 解決策:適切な切削条件を選定し、切削過程で発生する熱を適切に管理することが重要です。また、加工後に冷却を均等に行い、ひずみを抑えることが有効です。
- 問題3: 部品の破損
- 原因:過剰な応力や工具の不適切な使用が原因です。
- 解決策:適切な切削力と工具を使用し、過度の圧力がかからないようにすることが大切です。また、加工途中で部品に強い力がかからないように、加工条件を調整することが推奨されます。
機械的特性に関する問題への対応
A5056合金は高い機械的特性を持つものの、いくつかの問題が発生する可能性があります。これらの問題に対する対応策を以下にまとめます。- 問題1: 引張強度不足
- 原因:熱処理や加工の不具合が引張強度に影響を与える場合があります。
- 解決策:適切な熱処理プロセス(例えば、焼入れや焼戻し)を施すことにより、引張強度を向上させることが可能です。さらに、加工後のストレスを軽減するために、十分な冷却と休養期間を設けることが重要です。
- 問題2: 耐食性の低下
- 原因:表面処理の不完全さや腐食環境への長時間の曝露が原因です。
- 解決策:表面処理の再確認と、必要に応じてアルマイト処理やメッキ処理などの再施行を行い、耐食性を向上させます。また、長期間の使用においては定期的なメンテナンスと保護が重要です。
- 問題3: 摩耗や疲労による破壊
- 原因:過度の荷重や摩擦が繰り返し加わることにより、疲労破壊が発生します。
- 解決策:摩擦の低減や疲労強度を向上させるために、適切な表面処理を施すことが有効です。また、荷重の分散や適切な設計を行うことで、疲労に対する耐性を高めることができます。