A5052 H112とは?アルミ合金の種類とその用途を徹底解説
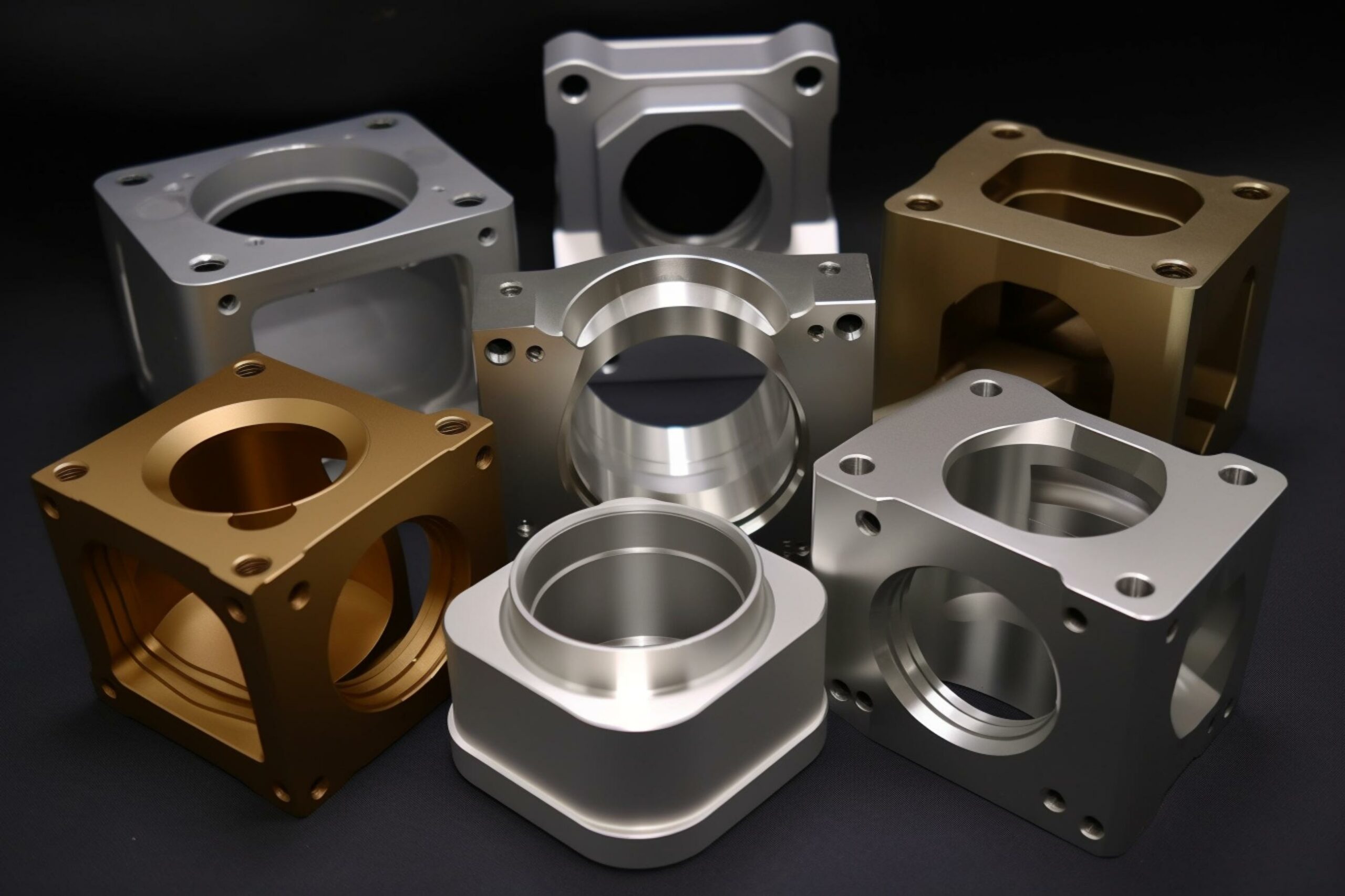
アルミニウム合金は、日常生活でも身近な材料であり、その中でもA5052 H112は特に注目される品種です。この記事では、A5052 H112とは何か、その特性や用途について詳しく解説していきます。
A5052 H112は、耐食性や可鍛性に優れた特性を持つアルミニウム合金であり、様々な産業分野で幅広く使用されています。その特性から、航空機や自動車、建築材料など、さまざまな製品に利用されています。
この記事では、A5052 H112の基本的な情報から始めて、その特性や用途について詳細に紹介していきます。アルミニウム合金に興味がある方やA5052 H112について知りたい方にとって、役立つ情報が満載です。さあ、A5052 H112の世界に一緒に深く探求してみましょう。
A5052 H112とは
A5052 H112は、アルミニウム合金A5052を特定の熱処理(H112)で仕上げたもので、耐食性や加工性に優れた特性を持っています。A5052合金は、主にマグネシウムを成分とし、軽量でありながら良好な強度を発揮します。特に腐食環境に強いことが特徴です。H112は、軽度の加工や熱処理を施した状態で、A5052の基本的な特性を維持しつつ、加工性が向上しています。
A5052 H112の基本的な特性
特性 | 内容 |
---|---|
引張強度 | 約 210 MPa |
耐食性 | 優れた耐食性(特に海水に強い) |
加工性 | 良好(押出し加工や成形が容易) |
溶接性 | 良好(溶接後も強度が維持されやすい) |
延性 | 約 12-20% |
硬度 | 45-60 HRB |
A5052 H112の化学成分と物理的性質
成分含有量 (%)
成分 | 含有量 (%) |
---|---|
アルミニウム (Al) | 95.7 – 98.5 |
マグネシウム (Mg) | 2.2 – 2.8 |
クロム (Cr) | 0.15 – 0.35 |
銅 (Cu) | 最大 0.1 |
鉄 (Fe) | 最大 0.4 |
シリコン (Si) | 最大 0.25 |
マンガン (Mn) | 最大 0.1 |
亜鉛 (Zn) | 最大 0.1 |
物理的性質
性質 | 値 |
---|---|
比重 | 約 2.68 g/cm³ |
熱伝導率 | 約 138 W/m·K |
融点 | 約 585-655°C |
A5052 H112のアルミ合金としての分類
A5052 H112は、「5000系」アルミニウム合金に分類されます。特にマグネシウム(Mg)が主成分で、優れた耐食性と高い加工性を誇ります。この系統は、海洋環境や化学工業環境に適した材料として使用されます。A5052はアルミニウム合金の中でも最も広く利用されており、船舶や機械構造物、化学設備の部品に多く使用されています。
アルミ合金の強度と耐久性
アルミ合金は軽量で優れた耐食性を持ち、さまざまな産業に利用されています。特にA5052 H112は、その特性から多くの産業で活用されていますが、強度と耐久性は設計や使用環境に大きく影響を与えます。強度は材料が外部からかかる力にどのように耐えるかを示す重要な指標です。以下では、アルミ合金、特にA5052 H112の強度と耐久性に関する要素、影響を与える要因、そして強度を向上させるための改善策についてさらに詳しく説明します。
強度とは何か
強度は、材料がどの程度外力に耐えることができるかを示す能力です。金属の強度にはさまざまな種類があり、それぞれ異なる力に対する耐性を示します。
- 引っ張り強度: 材料が引っ張られる力に対する耐性を示します。これは最も基本的な強度の指標であり、引っ張り試験で測定されます。
- 圧縮強度: 材料が圧縮される力に対する耐性を示します。圧縮強度は、材料が圧縮される状況での破壊や変形のしにくさを示します。
- 曲げ強度: 材料が曲げられる力に対する耐性を示します。曲げ強度は構造部材の曲げに対する耐性を示す重要な指標です。
これらの強度は、合金の組成や製造過程によって変わるため、用途に応じて最適な強度特性を持つ材料を選定することが重要です。
A5052 H112の強度と耐久性
A5052 H112は、良好な強度と高い耐食性を持つアルミ合金です。特に耐食性が要求される環境に適しており、塩害や化学薬品に対する耐性が高いです。以下の特性がA5052 H112の強度と耐久性に関与しています。
特性 | 詳細 |
---|---|
引張強度 | 約 210 MPa |
耐力 | 約 130 MPa |
延性 | 良好(良好な成形性と加工性を持つ) |
耐食性 | 海水や化学環境に対する高い耐性 |
硬度 | 比較的低いが、耐食性が重要な用途に適している |
耐摩耗性 | 一般的な使用においては十分であるが、過酷な摩耗環境には適さない場合がある |
A5052 H112は特に耐食性に優れており、塩害や化学薬品に対する耐性が高いため、海洋構造物や化学設備に適しています。しかし、他のアルミ合金に比べると引っ張り強度がやや低いため、強度が非常に重要な構造部材には適さない場合があります。
耐久性
耐久性とは、材料が長期間にわたって外的な要因にどれだけ耐えることができるかを示します。A5052 H112は、耐食性に優れており、特に腐食環境に強いため、耐久性が高いです。特に以下の要素が耐久性に影響を与えます。
- 耐食性: 海水や化学薬品に強いため、塩害の多い環境や化学設備に適しています。
- 高温耐性: 高温環境では強度が低下しやすいため、適切な合金選択が必要です。A5052 H112は、高温環境における使用には限界がありますが、耐食性が求められる環境には最適です。
- 疲労強度: 長期間にわたって繰り返し負荷がかかる環境では、疲労強度が重要です。A5052 H112は、疲労強度が高く、軽負荷環境での耐久性が優れています。
強度を左右する要因と改善策
アルミ合金の強度は、いくつかの要因によって決まります。以下の要因に注目して改善策を講じることで、A5052 H112の強度や耐久性を向上させることができます。
1. 合金の成分
- 要因: 合金の成分は強度に大きな影響を与えます。A5052 H112の合金は、主にマグネシウムを含み、耐食性を高めていますが、強度は他の合金に比べて低めです。例えば、銅を含む合金は強度が高くなりますが、耐食性が低下します。
- 改善策: 強度を向上させるためには、必要に応じて合金成分を変更することが考えられます。また、別の高強度のアルミ合金(例:A7075)を使用することも選択肢です。
2. 加工方法
- 要因: 加工方法によって強度が大きく変わります。冷間加工や熱処理によって、合金の強度を高めることができます。A5052 H112は比較的柔らかい合金ですが、冷間加工を施すことで強度を向上させることができます。
- 改善策: 適切な熱処理や冷間加工を施すことで、強度を向上させることができます。特に冷間加工後に適切な焼きなまし処理を行うことで、内部応力を解放し、強度の向上が見込まれます。
3. 製造過程での欠陥
- 要因: 鋳造や圧延などの製造過程で微細な欠陥が発生することがあります。これらの欠陥は、材料の強度を低下させ、耐久性に影響を与えることがあります。
- 改善策: 高精度な製造プロセスを採用し、欠陥を最小限に抑えることが重要です。また、非破壊検査(NDT)を行い、材料内の欠陥を検出して除去することも有効です。
4. 使用環境
- 要因: 高温や高圧環境では、アルミ合金の強度が低下することがあります。また、特定の環境(例:海水)では、腐食が進みやすくなります。
- 改善策: 高温環境や高圧環境での使用には、耐熱性が高いアルミ合金(例:A6061やA7075)を選ぶと効果的です。さらに、腐食が問題となる場合は、表面処理(アルマイト処理など)を行い、耐食性を向上させることが重要です。
5. 表面処理
- 要因: 表面処理が不十分な場合、腐食や摩耗が進行し、強度が低下します。特にA5052 H112は、耐食性が重要な用途で多く使用されますが、表面処理が不十分だとその特性を活かせません。
- 改善策: アルマイト処理や陽極酸化処理を施すことで、表面の耐食性を大幅に向上させることができます。これにより、長期にわたって強度を維持できるようになります。
アルミニウム合金の加工方法
アルミニウム合金の加工方法の基本
アルミニウム合金は、その軽量性、耐食性、加工性に優れているため、多様な製造工程で広く使用されています。特にA5052 H112は、加工性が良好で、さまざまな形状や製品に加工可能です。以下では、アルミニウム合金の主な加工方法と、A5052 H112の特性について説明します。
主な加工方法
加工方法 | 説明 | 特徴 |
---|---|---|
切削加工 | 旋盤やフライス盤を用いて形状を整える方法 | 高精度の部品を製造するために使用され、複雑な形状にも対応 |
圧延加工 | 鉄板やシートを薄く延ばす方法 | 大量生産に適し、薄板の製造に最適 |
鍛造加工 | 高温で圧力を加えて強度を高める方法 | 強度が求められる部品に利用される |
押出加工 | 金属を金型に押し込んで形状を作る方法 | 長尺製品や様々な断面形状の製造に使用される |
溶接加工 | 高い耐食性を維持しながら溶接する方法 | 強度を保ちながら接合できる技術が求められる |
A5052 H112の加工性
A5052 H112は、加工性が非常に優れている合金で、以下の特性があります。
- 良好な成形性: 引き伸ばしや圧延、曲げ加工が容易で、複雑な形状にも対応可能です。
- 高い耐食性: 加工後も耐食性が高く、特に海洋環境や化学プラントでの使用が多いです。
- 適度な強度: 引っ張り強度はやや低いですが、優れた加工性と耐食性のバランスを提供します。
A5052 H112の加工方法と特徴
加工方法 | 特徴 | 適用例 |
---|---|---|
切削加工 | 高精度で複雑な形状にも対応可能 | 精密部品、機械部品 |
圧延加工 | 薄板の製造に適し、大量生産に利用される | 薄板製品、包装材 |
押出加工 | 長尺製品を大量生産でき、断面形状のバリエーションが可能 | 窓枠、構造部材、配管 |
曲げ加工 | 柔軟に曲げられ、軽量で強度のある部品に適応 | 自動車部品、建築材料、家具のフレーム |
溶接加工 | 高い耐食性を保ちながら溶接可能 | 船舶、化学プラント設備、構造物 |
加工時の留意点
A5052 H112は優れた加工性を持ちますが、加工中に注意すべき点もあります。
曲げ加工時には過度の曲げが割れを引き起こすことがあります。適切な曲げ半径を守り、加工条件に配慮することが必要です。
切削時の熱処理:
加工時に発生する熱は、工具の摩耗を促進します。冷却液を使用することで摩耗を防ぐことができます。
熱処理を行わずに加工する場合、材料の硬度は低くなるため、切削時に引っかかりが発生しやすくなります。
溶接性:
A5052 H112は溶接性が良好ですが、過度な熱を加えると熱影響部で強度が低下するため、適切な溶接技術が重要です。
曲げ加工:
曲げ加工時には過度の曲げが割れを引き起こすことがあります。適切な曲げ半径を守り、加工条件に配慮することが必要です。
アルミニウムの溶接技術
アルミニウムはその軽量性、耐食性、加工性に優れており、さまざまな製品に使用されています。しかし、溶接には特有の難しさがあり、適切な技術と注意点が求められます。特に、A5052 H112のようなアルミニウム合金では、適切な溶接方法を選定し、品質を保つことが重要です。
溶接の基礎知識
アルミニウムの溶接は、他の金属と比べていくつかの特有の課題があります。
- 酸化皮膜: アルミニウムの表面には非常に強い酸化皮膜が形成されており、この皮膜は溶接を妨げる要因となります。溶接前に酸化皮膜を除去する必要があります。
- 熱伝導率が高い: アルミニウムは熱を素早く伝導するため、溶接時に熱集中を防ぐための工夫が求められます。
- 低い融点: アルミニウムの融点は比較的低いため、溶接時の温度管理が重要です。
A5052 H112の溶接方法
A5052 H112は、優れた耐食性と良好な加工性を持つアルミニウム合金であり、以下の溶接方法が適しています。
溶接方法 | 特徴 | 適用例 |
---|---|---|
TIG溶接 | 非常に精密な溶接が可能で、アルゴンガスを使用して酸化を防ぎます。薄い材料や高精度が求められる部品に適しています。 | 自動車部品、航空機部品、精密機器の製造 |
MIG溶接 | 高速で効率的に溶接が行える方法で、連続的な溶接が可能です。厚い部材にも対応できます。 | 機械部品、大型構造物 |
フラッシュ溶接 | 接合部分を高温で加熱し、圧力をかけて結合する方法です。部品が接触する面で均等に熱を伝えます。 | 金属加工業での使用、車両部品など |
スポット溶接 | 部品を圧力と電流で溶接する方法です。薄板の接合に適しています。 | 車体部品の組み立て、薄板の接合 |
溶接時の注意点とテクニック
A5052 H112の溶接には、いくつかの注意点と技術的な工夫が必要です。
- 酸化皮膜の除去: 溶接前に酸化皮膜をしっかりと除去することが重要です。酸化皮膜をそのままにして溶接すると、接合部の品質が低下します。例えば、研磨や酸処理で表面を清掃します。
- 熱管理: アルミニウムは熱伝導性が高いため、溶接時に熱が過度に集中すると部材が変形したり、溶接不良が発生したりします。冷却を適切に行い、熱膨張を抑えることが重要です。
- 溶接速度の調整: 溶接速度が速すぎると、溶け込みが不十分で強度が不足します。逆に遅すぎると過度の熱が加わり、変形や溶接不良を引き起こす可能性があります。適切な速度を保ちながら溶接を行うことが求められます。
- ガス選定: TIG溶接やMIG溶接では、使用するガス(主にアルゴンガス)の流量と純度が重要です。高品質な溶接を行うためには、適切なガスの供給が必須です。
- 適切な電流設定: A5052 H112に適した電流設定を使用することで、溶接部の品質を保つことができます。低すぎる電流設定では溶け込みが不十分、逆に高すぎると溶けすぎてしまうため、試験を行いながら調整します。
アルミニウム製品の耐食性とA5052 H112
アルミニウムは、その軽量性、強度、そして優れた耐食性から多くの産業で利用されています。特に、A5052 H112はその優れた耐食性により、厳しい環境でも長期間にわたって高い性能を発揮します。本稿では、腐食の基本的なメカニズム、A5052 H112の耐食性の特徴、そして耐食性を強化するための方法について詳しく解説します。
腐食とは何か?
腐食は、金属が周囲の環境と反応し、物理的・化学的特性が変化する現象です。特に酸素や水分と反応して金属が酸化することにより、表面が劣化し、金属の強度が低下したり、美観が損なわれたりします。
腐食の主なメカニズム
メカニズム | 説明 |
---|---|
酸化反応 | アルミニウムは酸素と結びついて酸化アルミニウム(Al₂O₃)を形成します。この酸化膜は硬く、金属表面を保護しますが、過酷な環境下では腐食が進行することがあります。 |
電気化学的腐食 | 異なる金属が接触すると、電位差が生じて電気化学的腐食が発生します。この腐食は、特に異種金属間の接触によって進行します。 |
A5052 H112の耐食性の特徴
A5052 H112はマグネシウムを主成分とするアルミニウム合金であり、非常に優れた耐食性を持っています。この耐食性に寄与する特性を以下にまとめます。
A5052 H112の耐食性の特徴
特性 | 詳細 |
---|---|
酸化皮膜の形成 | アルミニウムは酸素と反応して酸化アルミニウム膜(Al₂O₃)を形成します。この膜は自然に発生し、表面を保護する役割を果たします。 |
耐塩害性 | A5052 H112は塩分が多い環境、特に海水環境において非常に強い耐塩害性を示します。これは海洋構造物や船舶などに最適です。 |
高い耐酸性 | A5052 H112は酸性環境においても耐性が高く、化学工業や食品加工業で多く使用されます。酸性や化学薬品への耐性が強いのが特徴です。 |
A5052 H112の耐食性を高める方法
A5052 H112の耐食性をさらに強化するためには、以下の方法が有効です。これらを組み合わせることで、より過酷な環境でもその耐久性を向上させることが可能です。
1. 表面処理
方法 | 説明 |
---|---|
陽極酸化 | アルミニウムの表面に強固で厚い酸化膜を形成させ、耐食性を大幅に向上させる方法です。この膜は高い硬度を持ち、化学的にも強い耐性を示します。 |
化学的処理 | クロム酸塩や亜鉛処理などの化学的表面処理により、アルミニウムの表面に保護膜を形成し、腐食に対する耐性を強化します。 |
2. コーティング
方法 | 説明 |
---|---|
樹脂コーティング | ポリウレタンやエポキシ樹脂をアルミニウム合金に塗布することで、物理的な保護層を形成し、化学的腐食から保護します。 |
金属コーティング | 亜鉛やニッケルなどの金属でアルミニウム表面をコーティングすることで、耐食性が大幅に向上します。特に亜鉛メッキは、鉄鋼の耐腐食性を向上させるために利用されます。 |
3. 環境管理
方法 | 説明 |
---|---|
湿度や塩分濃度の管理 | 腐食を引き起こす原因となる湿度や塩分濃度を適切に管理することが重要です。特に海上環境では塩害が発生しやすいため、これらの要因を管理することが耐食性を高めます。 |
化学的防食 | 酸性や塩基性の環境において、化学的に中和剤を使用してpHバランスを調整し、アルミニウムの腐食を防ぐ方法です。 |
4. 設計段階での腐食防止
方法 | 説明 |
---|---|
設計時に腐食を考慮 | 異種金属が接触しないように設計を行い、電位差を防ぐことで、電気化学的腐食を防止します。 |
水分の排除設計 | 水分が溜まりやすい場所には排水孔を設け、適切な排水設計を施すことで、水分の蓄積を防ぎ、腐食を予防します。 |