アルミの強度と加工性を解説!A5052 H32 H34の特性と用途
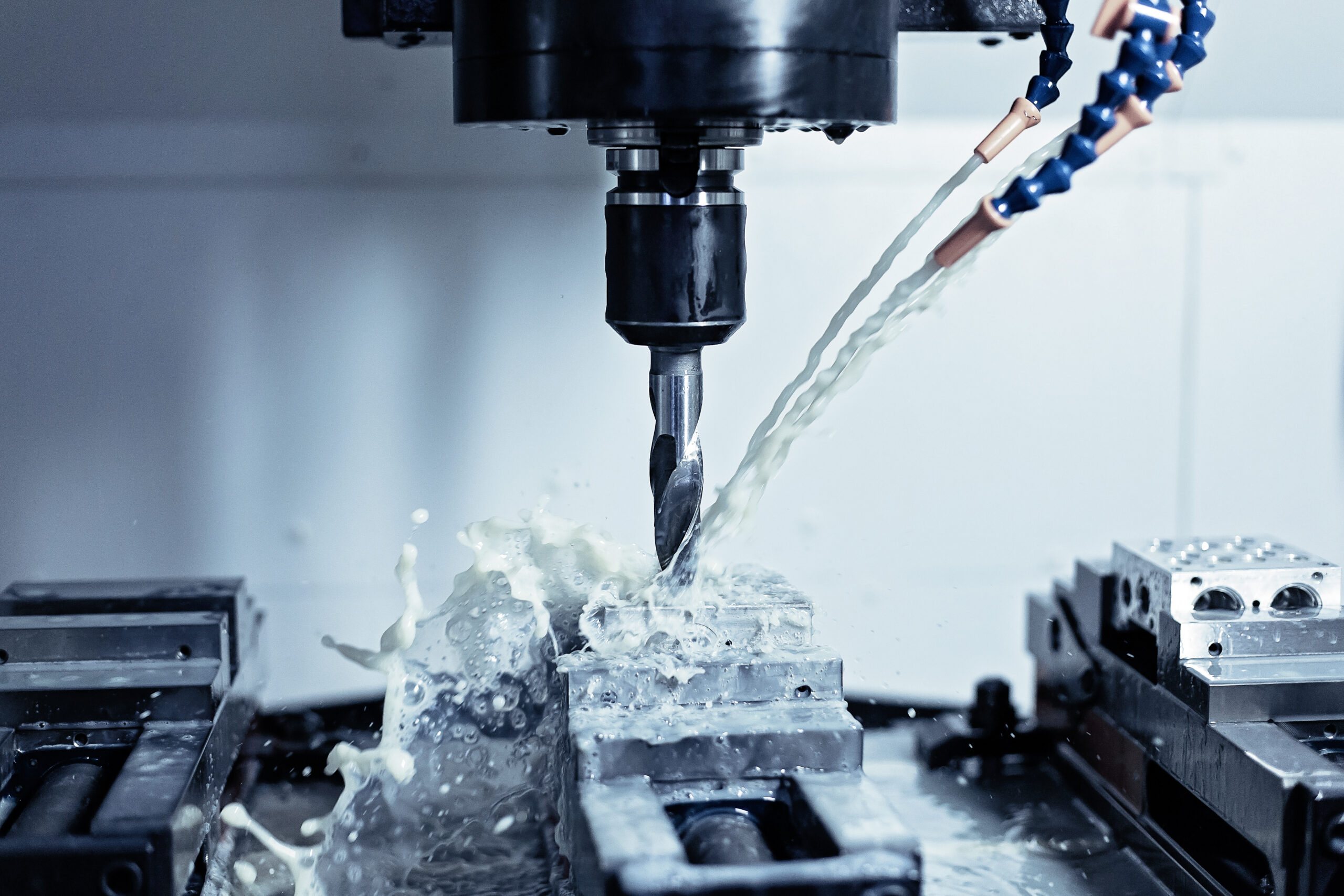
アルミは現代の産業において欠かせない素材となっています。特に、A5052という合金はその優れた特性で注目を集めています。また、H32やH34の表記は耳にしたことがある方も多いかもしれませんが、その意味や特性について理解しているでしょうか?
本記事では、アルミの強度と加工性に焦点を当て、A5052の特性や用途について詳しく解説していきます。さらに、H32とH34の違いやそれぞれの特長についても掘り下げていきます。アルミニウム合金に関心を持ち、その知識を深めたい方々にとって、貴重な情報が満載の記事となっています。アルミニウムの世界に足を踏み入れる前に、ぜひこのガイドをご覧になって、理解を深めてみてください。
アルミ合金A5052の基本的理解
アルミ合金A5052とは
A5052は、マグネシウムを主成分とするアルミニウム合金で、優れた耐食性と機械的特性を備えています。これにより、海洋環境や化学工業、航空機、車両部品などで広く使用されています。A5052は、溶接性が良好で加工性も高く、多用途に適しています。
主な特徴
特徴 | 詳細 |
---|---|
成分 | アルミニウム(主成分)、マグネシウム(2.2~2.8%)、その他微量元素 |
耐食性 | 塩水環境や海洋環境でも耐久性が高く、腐食に強い |
強度 | 中程度の強度で、耐久性が必要な部品に最適 |
加工性 | 良好な加工性を持ち、切削、溶接、曲げ加工が容易 |
重量 | 軽量でありながら高い強度を保持 |
用途 | 船舶部品、航空機部品、自動車部品、建築材料など |
A5052の化学的組成
成分 | 含有量 (%) |
---|---|
アルミニウム (Al) | 残りの大部分 |
マグネシウム (Mg) | 2.2% – 2.8% |
クロム (Cr) | 0.15% – 0.35% |
鉄 (Fe) | 最大 0.4% |
マンガン (Mn) | 最大 0.1% |
シリコン (Si) | 最大 0.25% |
銅 (Cu) | 最大 0.1% |
A5052合金の主成分であるマグネシウムは、合金の耐食性を高め、特に海水や塩水環境下での使用に適しています。クロムも少量含まれ、さらに耐食性を向上させます。
A5052 H32とH34とは
A5052には異なる硬化状態があり、H32とH34はそれぞれ次のような特徴を持っています:
- H32: 半硬化状態。良好な強度と加工性を提供し、一般的な用途に適しています。
- H34: 強化状態。さらに高い強度を持ち、過酷な条件下での使用に適しています。
H32は一般的な用途、H34はより高い強度が求められる用途に適しています。用途に応じて適切な熱処理状態を選ぶことが重要です。
H32とH34の違い
特性 | A5052 H32 | A5052 H34 |
---|---|---|
強度 | 比較的柔らかく、曲げやすいが強度も高い。軽量な構造部品に適している。 | より高い強度を持ち、重い荷重がかかる部品に適している。 |
加工性 | 深絞り加工や複雑な形状の加工がしやすい。 | 加工がしやすく、特に強度重視の部品に適する。 |
耐食性 | 高い耐食性を持ち、過酷な環境でも使用可能。 | 耐食性はH32と同等であり、過酷な環境でも使用可能。 |
用途 | 自動車のボディパネル、航空機部品、船舶部品、液晶テレビのフレームなどに使用。 | 主に強度が求められる部品に使用される。例えば、重機や構造部材。 |
A5052の特性と選定ポイント
- 耐食性: 海水や塩水環境に強い。
- 加工性: 良好で、切削や溶接が容易。
- 強度: 適度な強度を持ち、一般的な構造用途に最適。
- 使用環境: 航空機、車両部品、化学プラント設備などで使用。
A5052は耐食性が高く、特に過酷な環境下での使用に適しているため、選定時には使用する環境や求められる強度を考慮することが重要です。
アルミ合金A5052の特性
A5052の機械的特性
アルミ合金A5052は、その強度と加工性のバランスが優れており、さまざまな産業で広く使用されています。特に、A5052のH32とH34という表記は、それぞれの硬度と強度を示しており、H34はH32よりも強度が高く、硬い特性を持っています。以下に、A5052の主要な機械的特性を示します。
A5052の機械的特性
特性 | H32 | H34 |
---|---|---|
引張強度 | 約 210~230 MPa | 約 250 MPa |
降伏強度 | 約 180 MPa | 約 230 MPa |
伸び | 約 12%~20% | 約 12%~18% |
硬度 | 約 60~70 HRB | 約 75~85 HRB |
比重 | 約 2.68 | 約 2.68 |
引張モジュラス | 約 70 GPa | 約 70 GPa |
特徴と効果
- 引張強度:A5052は、強度において優れた特性を持ち、H32の引張強度は約210~230 MPa、H34は約250 MPaとなっており、H34の方がより強力です。この特性により、特に船舶、航空機、自動車の部品において、強度が要求される場所での使用に適しています。
- 降伏強度:降伏強度は、材料が永久的に変形し始める前に耐えられる最大応力を示し、H34の降伏強度はH32よりも高いため、H34はより高い荷重に耐えることができます。
- 伸び:伸びは、材料が破断する前にどれだけ伸びるかを示す指標であり、A5052はその加工性が高く、特に曲げ加工や溶接が容易です。H32の伸び率はH34に比べてやや高いため、柔軟性を活かした加工が可能です。
- 硬度:H32とH34の硬度差は、H34が高い強度と硬さを持ち、より耐摩耗性が高いことを意味します。これにより、H34は高負荷や摩擦が多い環境での使用に適しています。
- 比重と引張モジュラス:A5052はアルミ合金であり、比重は約2.68と軽量で、引張モジュラスは70 GPa程度であるため、軽量かつ強度のある部品を作成することができます。
用途
A5052はその優れた機械的特性から、以下のような用途に広く使用されています。
A5052の耐食性と耐久性
A5052はアルミニウム合金の一種であり、優れた耐食性と耐久性を誇ります。特に、A5052のH32とH34のバリエーションは、それぞれ異なる特性を持ち、用途に応じた選択が可能です。
- 耐食性: A5052は、特に塩水環境に強い特性を持ち、海洋や化学プラントでの使用に最適です。そのため、船舶や防錆が求められる環境で多く利用されています。
- 耐久性: A5052は、優れた強度と耐久性を兼ね備えており、軽量ながらも構造的に高い耐久性を提供します。航空機や自動車の部品に利用され、長期間の使用にも耐えられます。
これらの特性により、A5052は航空機のボディパネルや自動車のボディパーツなど、強度と軽量性が要求される製品に広く使用されています。例えば、飛行機の翼や自動車のドアパネルなどが代表的な用途です。
H32とH34の強度比較
A5052アルミ合金は、H32とH34の異なる状態で提供され、それぞれに特有の強度と加工性があります。以下の表で、H32とH34の強度を比較し、特性の違いを明確にします。
特性 | H32 | H34 |
---|---|---|
引張強度 | 約 210~230 MPa | 約 250 MPa |
降伏強度 | 約 180 MPa | 約 230 MPa |
伸び | 約 12%~20% | 約 12%~18% |
硬度 | 約 60~70 HRB | 約 75~85 HRB |
引張強度
- H32: 引張強度は約210~230 MPaで、柔軟性があり、加工性に優れています。これにより、深絞りや曲げ加工が求められる部品に適しています。
- H34: 引張強度は約250 MPaで、より強度が高く、特に強度が求められる構造部品に最適です。
降伏強度
- H32: 降伏強度は約180 MPaで、加工や成形が容易で、特に形状変更が必要な部品に適しています。
- H34: 降伏強度は約230 MPaで、高い荷重に耐え、強靭な部品に向いています。
伸び
- H32: 伸びは約12%~20%と高く、柔軟性に優れています。このため、曲げ加工や深絞り加工に適しています。
- H34: 伸びは約12%~18%でやや低くなりますが、その分、強度が高いため、耐久性が求められる部品に最適です。
硬度
- H32: 硬度は約60~70 HRBで、加工がしやすく、特に溶接や成形に向いています。
- H34: 硬度は約75~85 HRBで、高い耐摩耗性を持ち、摩擦の多い環境での使用に最適です。
用途における適用
H32
- 加工性が高く、柔軟性に優れるH32は、曲げ加工や深絞り加工が必要な部品に適しています。具体的な用途としては、家電製品、薄板部品、自動車の内装部品などが挙げられます。
H34
- H34は高い強度を持ち、耐久性が求められる部品に適しています。特に、強度が重要な構造部品に使用され、船舶や航空機、自動車のボディパネル、建築部材などに広く使用されています。
A5052のH32とH34は、それぞれ異なる強度と加工特性を活かし、製品設計や製造において最適な選択をするための重要な材料です。
アルミ合金A5052の加工性
加工の難しさとその原因
アルミ合金A5052は、他のアルミ合金に比べて加工が容易な素材とされていますが、それでもいくつかの加工における難しさが存在します。これらの難しさの主な原因として、次の点が挙げられます。
- 硬さと強度: A5052は比較的強度が高く、耐久性にも優れていますが、この特性が加工時に若干の難しさを生むことがあります。特に機械加工や切削時に適切な工具や条件を選ばないと、工具の摩耗が早くなったり、加工面が粗くなったりすることがあります。
- 熱膨張: 加熱時の熱膨張が原因で、非常に高温での加工では材料が歪むことがあります。これにより、加工精度を保つことが難しくなる場合があります。
- 切削時の熱の影響: A5052の切削時に発生する熱が材料に与える影響もあります。温度の上昇により材料が変形しやすくなるため、切削速度や冷却方法に注意を払う必要があります。
A5052の加工方法とその適用
アルミ合金A5052は、加工方法において多くの選択肢があります。以下は、A5052の代表的な加工方法とその適用例です。
加工方法 | 適用例 |
---|---|
切削加工 | A5052の機械加工(フライス加工、旋盤加工、ボーリング)に使用される。高精度な部品の製造が可能。 |
圧延加工 | 薄板や板金製品の製造に適用。耐食性を活かして建築や自動車、船舶業界での使用が多い。 |
溶接加工 | A5052は溶接性に優れており、航空機や自動車の部品製造に使用される。 |
押出加工 | パイプ、型材、フィンなどの部品製造に使用される。特に自動車業界や冷却器などに活用される。 |
A5052の加工方法とその適用
A5052の加工においては、以下の点が考慮されています:
- 切削加工: A5052は比較的加工が容易ですが、冷却液を使用して熱を抑えながら行うことが重要です。フライス加工や旋盤加工で高精度を求められる部品が製造されます。
- 圧延加工: 薄板や板金に加工されることが多く、建材や船舶、自動車のボディパーツなどで利用されます。特に、耐食性と成形性が求められる製品に適しています。
- 溶接加工: アルミ合金A5052は溶接性が良好で、TIG溶接やMIG溶接など、異なる溶接技術が適用されます。特に自動車部品や航空機の部品に多く使用されています。
- 押出加工: A5052は押出加工にも適しており、これにより高精度なパイプや型材を製造できます。冷却器のフィンなど、熱交換機構が必要な製品でよく使用されます。
アルミ加工の基本
アルミ加工の一般的な手法
アルミは加工が比較的容易な素材であり、さまざまな手法が存在します。代表的な加工方法は以下の通りです。
加工方法 | 概要 |
---|---|
切削加工 | フライス盤や旋盤を使用して、アルミを削り取る方法。精密な形状の部品を作成できます。 |
圧延加工 | アルミを圧力で引き延ばす方法。板やシートを製造するためによく使用されます。 |
溶接加工 | アルミを溶かして接合する方法。特に自動車や航空機部品に多く使用されます。 |
押出加工 | アルミを型に押し出す方法。パイプや型材の製造に用いられます。 |
鋳造加工 | アルミを溶かし型に流し込んで固める方法。複雑な形状を製造するのに適しています。 |
アルミ加工時の注意点
アルミは軽量であり、比較的柔らかいため加工が容易ですが、いくつかの注意点があります。
- 温度管理: 加工中に過度な熱が加わると、アルミの性質が変わり、軟化してしまうことがあります。冷却液や適切な温度管理が重要です。
- 工具の摩耗: アルミは比較的柔らかいため、使用する工具が摩耗しやすいです。切削工具の選定や定期的な交換が必要です。
- 表面処理の影響: アルミには酸化膜が自然に形成されますが、加工中に表面が傷つくと腐食の原因となります。加工後の表面処理(陽極酸化など)が推奨されます。
- 切削速度: 高速で切削を行うとアルミが溶ける可能性があるため、適切な切削速度を選定することが重要です。
加工ミスを避けるためのポイント
アルミ加工時に発生しがちなミスを避けるために、以下のポイントを押さえておくことが重要です。
- 適切な切削条件を設定する: アルミの加工には適切な切削速度、送り速度、切削深さが必要です。条件設定を誤ると、材料が焼けたり、表面に不良が出たりすることがあります。
- 工具の選定を慎重に行う: アルミ専用の工具を選定し、鋭利で摩耗に強いものを使うことで、加工ミスを減らせます。
- 定期的なメンテナンス: 加工機や工具の定期的なメンテナンスを行い、正常な状態で加工を行うことが大切です。劣化した機器を使うと不良が発生する可能性が高くなります。
- 冷却液の適切な使用: 加工中に冷却液を使用することで、工具の温度上昇を防ぎ、アルミの変形を抑えることができます。冷却液の量や種類も選定が必要です。
- 加工順序の計画: 加工時に順序を間違えると、精度や仕上がりに問題が発生することがあります。予めしっかりとした加工計画を立て、必要な手順を踏んで加工を行いましょう。
アルミ合金加工のコツとテクニック
効率的な加工方法の選定
アルミ合金の加工には、目的に応じた効率的な加工方法を選ぶことが大切です。以下のポイントを参考にすることで、時間とコストを削減できます。
加工方法 | 効率的な選定理由 |
---|---|
切削加工 | 高精度な部品が必要な場合、特に重要。最適な工具と切削条件で効率的に加工できます。 |
圧延加工 | 大量生産に最適。比較的低コストで大量の板やシートを製造できます。 |
溶接加工 | 複雑な形状を求められる場合に効率的。適切な溶接機を選定し、溶接速度を最適化することでコスト削減が可能です。 |
押出加工 | パイプや型材の大量生産に適しています。一定の断面形状を持つ製品の製造に効率的です。 |
加工精度を高める方法
アルミ合金は軽量で加工しやすい素材ですが、その特性を最大限に活かすためには適切な加工方法が求められます。以下にアルミ合金加工のコツと、加工精度を高めるためのテクニックを紹介します。
1. 適切な工具選び
用途 | 推奨工具 |
---|---|
切削加工 | 高速度鋼(HSS)または超硬工具 |
フライス加工 | 鋭利なカッターを使用し、工具の摩耗を最小化 |
旋盤加工 | スピンドル回転数を高く設定し、安定した切削 |
穴あけ加工 | 超硬ドリルビットを使用 |
アルミ合金加工には、切削工具の選定が重要です。鋭利な刃先を持つ工具を使用することで、加工中の摩擦を減らし、精度を高めることができます。超硬工具や高速度鋼(HSS)は、アルミ合金の特性に合った切削性能を発揮します。
2. 適切な切削速度と送り速度
アルミ合金は比較的軟らかく、金属の切削速度や送り速度が適切でないと、加工精度が低下したり、工具が早く摩耗したりします。一般的に、切削速度は高速に設定し、送り速度は適度に調整します。具体的には:
- 切削速度:高速度で、アルミ合金の熱を迅速に逃がし、切削面の品質を向上させます。
- 送り速度:適切な送り速度を設定することで、切削の摩擦を減らし、切削面の荒れを防ぎます。
3. クーラントの使用
アルミ合金は加工時に熱を持ちやすく、適切な冷却が必要です。クーラントを使用することで、加工中の工具温度を下げ、工具の摩耗を減少させ、加工精度を保つことができます。切削油やエアブローで冷却し、熱膨張を抑えることが重要です。
4. 加工時の振動抑制
加工中に発生する振動は、加工精度を低下させる原因となります。振動を抑えるためには、以下の方法を採用することが効果的です:
- 安定した固定:素材や工具をしっかりと固定し、加工中に動かないようにする。
- 適切な切削条件の設定:過度な切削力を避け、振動が発生しないようにする。
- 工具の剛性を高める:加工中の工具の振動を減らすために、剛性が高い工具を使用します。
5. 加工後の仕上げ処理
加工後に表面を仕上げることで、最終的な精度が大きく向上します。以下の方法を使用して、仕上げ処理を行うことができます:
- 研磨:表面の微細な傷や不均一性を取り除き、仕上がりを滑らかにします。
- バリ取り:加工中に発生したバリを除去することで、製品の精度が向上します。
- 表面処理:アルマイト処理や塗装などで、表面の強度や耐腐食性を向上させます。
6. 定期的な工具のメンテナンス
加工精度を保つためには、工具のメンテナンスが欠かせません。定期的に工具の刃先をチェックし、摩耗している場合は早めに交換しましょう。また、加工後には工具を清掃し、切削油が残らないようにして次回の使用に備えます。
まとめ
アルミ合金の加工精度を高めるためには、適切な工具選びや切削条件の設定、クーラントの使用など、細かな配慮が求められます。これらのコツとテクニックを実践することで、精度高く、高品質な加工を実現できます。
加工コストを抑えるポイント
アルミ合金の加工において、コストを抑えるためにはいくつかの重要なポイントを押さえる必要があります。効率的な加工方法や材料の選定、設備の活用などが、最終的なコスト削減に繋がります。以下の方法で、アルミ合金の加工コストを抑えることができます。
1. 適切な材料選定
材料選定はコスト削減に直結します。以下の表は、異なるアルミ合金の特性と適切な利用シーンを示しています。
材料 | 特徴 | 利用シーン |
---|---|---|
A5052 | 高い強度と優れた加工性を持つ | 船舶、航空機、自動車部品 |
A6061 | より高い強度と耐食性が必要な場合に最適 | 機械部品、構造物 |
A3003 | 軽量でコストが低く、加工が簡単 | 家電製品、屋根材 |
不要に高性能な材料を使用すると、コストが上がるため、必要な特性を満たす材料を選定することでコスト削減に繋がります。
2. 加工方法の最適化
加工方法の選択により、コストを大きく削減できます。特に以下のポイントが重要です:
- 自動化: 自動化された設備を使用することで、加工精度を保ちながら人件費を削減できます。
- 連続加工: 大量生産が可能な場合、連続加工を行うことで効率が上がり、単位あたりのコストが低減します。
- 最適な切削条件: 切削速度や送り速度を最適化することで、工具の摩耗を減らし、長時間使用が可能になり、工具交換頻度を減らすことができます。
3. 工具の選定とメンテナンス
工具選びも重要なコスト削減要素です。以下の表では、工具の種類とその利点、使用時の注意点を示します。
工具種類 | 利点 | 使用時の注意点 |
---|---|---|
超硬工具 | 高耐久性で長寿命、加工精度が高い | 初期投資が高いが長期的にコスト削減可能 |
高速度鋼工具 | コストが低く、汎用性が高い | 定期的なメンテナンスが必要 |
超硬工具は初期投資が高いものの、長寿命で工具交換頻度が少なくなるため、長期的にはコスト削減になります。一方、高速度鋼工具は安価であり、比較的柔軟に対応できますが、定期的なメンテナンスと交換が必要です。
4. クーラントと冷却方法の工夫
クーラントの使用は、工具の寿命を延ばし、加工中の熱を効果的に管理するために欠かせません。効率的な冷却方法を採用することで、過剰な冷却剤の使用を避け、コストを削減することができます。
- エアブローシステム: 冷却剤を使わず、空気で冷却を行う方法も効果的です。
- 循環システム: クーラントの再利用システムを使用することで、廃棄物の削減とコスト削減が可能です。
5. 不良品の削減
加工中に発生する不良品の削減もコスト削減に繋がります。精度の高い設備や管理体制を整えることで、不良品の発生を減らし、余分なコストを抑えることができます。
- 品質管理の徹底: 製品ごとに品質管理を行い、トラブルの発生を防ぎます。
- プロセス改善: 工程ごとの問題点を洗い出し、改善することで効率を向上させ、不良品を減らします。
6. 効率的な工程配置
効率的な生産ラインの設計により、材料や製品の移動を最小限に抑え、無駄を減らすことができます。これにより、時間の節約とともにコスト削減が実現できます。