“高強度A5056合金の切削加工 – よくある質問とその解決策”
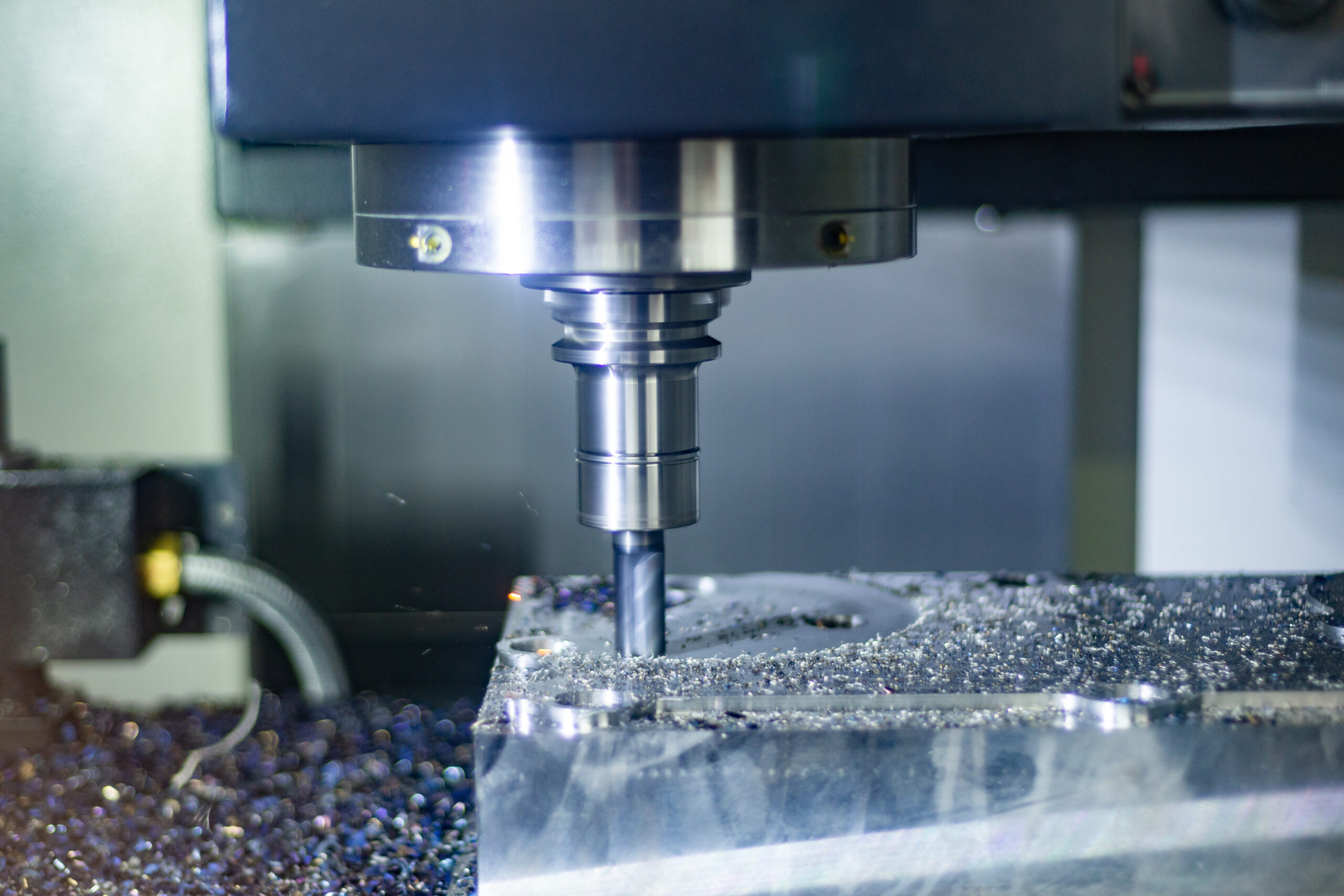
高強度A5056合金の切削加工に関するよくある疑問について知りたいですか?どのように切削性を向上させるか悩んでいますか?それなら、この記事がお役に立つかもしれません。
A5056合金は、その特性から切削加工が一筋縄ではいかないことが知られています。しかし、正しい手法を理解し、適切な対処法を知ることで、高強度A5056合金の切削性を向上させることができます。
この記事では、A5056合金の切削加工に関するよくある質問やその解決策について詳しく解説しています。高強度A5056合金の切削性について理解を深め、効果的な加工方法を見つけるための手助けとなるかもしれません。
目次
アルミニウムA5056の基本特性
アルミニウムA5056は、主に耐食性や高強度が求められる分野で使用される合金で、主成分はアルミニウムとマグネシウムです。アルミニウム合金の中でも優れた機械的特性を有し、特に耐腐食性や耐摩耗性に優れています。一般的に航空機の構造部品や船舶、化学機器など、過酷な環境下で使用される部品に使用されます。特に耐食性に関しては、海水や塩分を含んだ環境においても高い耐久性を発揮します。A5056の比重について
アルミニウムA5056の比重は約2.66 g/cm³です。これは純粋なアルミニウム(比重2.70 g/cm³)よりも若干軽い値ですが、アルミニウム合金の中でも一般的な範囲に収まります。比重が低いため、A5056は軽量であり、構造部材として使用する際には、機器や輸送機器の重量を軽減する効果があります。特に航空機や船舶、車両など、軽量化が求められる部品に非常に適しています。 軽量である一方、強度や耐久性も高いため、輸送機器や高強度が求められる部品にもよく使用されます。合金の比重が低いため、長期的な使用においても腐食に対する耐性と合わせて、軽量化を実現することが可能です。A5056の融点と耐熱性
- 融点:アルミニウムA5056の融点は、約600°Cから650°Cの範囲にあります。これは純粋なアルミニウムの融点(660°C)に非常に近い値であり、アルミニウム合金としてはやや低めの融点です。しかし、A5056は合金特性により、融点が少し低くなる一方、耐熱性に関しては非常に優れた特性を持っています。
- 融点が比較的低いため、加工がしやすく、熱処理によって強度を高めることができます。たとえば、熱間加工や冷間加工を行うことで、製品の機械的特性や耐食性をさらに向上させることが可能です。
- 耐熱性:A5056は高温に対して一定の耐性を持っていますが、温度が500°Cを超えると強度が急激に低下する可能性があります。最適な使用温度範囲は、常温から約200°Cまでです。特に、熱間作業や高温環境下での使用では、適切な冷却や熱処理が必要となります。A5056は、極端に高温の環境下で使用される場合には、その強度を保持するための特別な設計やコーティングが求められます。
- たとえば、航空機や車両の部品においては、高温での長時間の使用において強度が低下しないように設計されています。また、溶接や高温環境での加工時には、耐熱性を保つための適切な技術が必要です。
- 耐腐食性:A5056は優れた耐食性を持つため、海水や湿気の多い環境においても非常に安定した性能を発揮します。特に船舶や海洋機器など、塩水にさらされる環境でも腐食しにくいため、長期間の使用でも高い耐久性を維持します。アルミニウムの中でも耐食性が優れたA5056は、化学プラントや環境に優れた耐腐食性が求められる分野で広く使用されます。
A5056のその他の特性
- 溶接性:A5056は非常に良好な溶接性を持ち、TIG溶接やMIG溶接など、多様な溶接技術に対応できます。溶接後の耐食性も高く、結晶粒が粗くなることなく、しっかりとした溶接部を作ることが可能です。
- 加工性:加工性も良好で、冷間加工や熱間加工がしやすいことから、様々な形状への加工が可能です。特に薄板の加工や複雑な形状への対応力が強いです。
- 機械的特性:引張強度、耐摩耗性、耐久性に優れ、衝撃や振動の多い環境でもその特性を発揮します。特に航空機や自動車部品のように高強度を必要とする部分において非常に重宝されています。
A5056合金とA5052合金の比較
A5056合金とA5052合金は、どちらもアルミニウムを主成分とした合金で、特に優れた耐食性を持つことで知られています。しかし、これらの合金は異なる特性を持ち、使用される用途にも違いがあります。以下では、A5056とA5052の成分、特性、用途について詳しく比較します。A5056とA5052の成分と特性
A5056合金の成分と特性
- 主成分:A5056合金はアルミニウムを主成分とし、約4.5%のマグネシウムを含んでいます。これにより、強度と耐腐食性に優れ、特に海水や湿気の多い環境でも高い耐久性を発揮します。
- 特性:
- 高強度と耐腐食性
- 良好な溶接性
- 複雑な形状に加工可能
- 高い耐熱性(最大200°C程度まで)
- 良好な機械的特性(特に引張強度と耐摩耗性)
A5052合金の成分と特性
- 主成分:A5052合金もアルミニウムとマグネシウムを含む合金ですが、A5052のマグネシウム含有量は約2.5%と、A5056より低いです。これにより、強度はやや低いですが、優れた成形性と溶接性を有しています。
- 特性:
- 優れた耐腐食性(特に海水や化学環境下で強い)
- 高い成形性と加工性
- 良好な溶接性
- 低温環境でも強度を維持
- 中程度の強度
二つの合金の用途と適用分野
A5056の用途と適用分野
- 航空機部品:A5056は高強度と耐腐食性を持つため、航空機の構造部材やエンジン部品に適しています。
- 船舶:海水に強い耐腐食性を発揮するため、船舶の外部構造やプロペラの部品に使用されます。
- 化学プラント:化学薬品や酸に耐えるため、化学機器やタンクにも利用されます。
- 高強度が求められる部品:自動車のエンジン部品や構造部材、スポーツカーのパーツなどにも使われます。
A5052の用途と適用分野
- 船舶構造:A5052も船舶に使用されますが、特に耐腐食性と加工性が重要な部分に使われます。
- 自動車の部品:薄い板金部品や構造部品、車両の外装パーツなどにも利用され、成形がしやすい特性を活かしている。
- 製缶業界:A5052は非常に良好な成形性と加工性を持ち、製缶業界で使用されることが多いです。
- 冷蔵設備:低温環境での使用に強い特性を持つため、冷蔵設備や冷却機器の製造に適しています。
A5056合金の切削加工性
A5056合金は、優れた耐腐食性と強度を持ち、多くの産業で利用されていますが、切削加工性については特定の注意が必要です。以下では、A5056の切削加工性の概要、切削工具の選定、切削条件、さらに切削における問題点とその対策について解説します。A5056の切削加工性の概要
A5056は、アルミニウム合金の中でも強度が高く、耐食性に優れていますが、切削加工を行う際には以下のような特性があります。- 切削性:A5056は比較的柔らかい金属であり、切削性は良好です。加熱しても硬化しにくいため、低速での切削でも問題は少ないです。
- 熱伝導性:アルミニウム合金は熱伝導性が高いため、切削時に発生する熱を速やかに拡散させることができます。これにより切削中の温度上昇を抑えることが可能です。
- 粘着性:アルミニウム系の合金は、切削工具に対して粘着しやすいため、切削工具にアルミニウム片が付着しやすいです。この現象は工具の摩耗を早めるため、注意が必要です。
切削工具の選定と切削条件
切削工具の選定
A5056合金を切削する際には、適切な切削工具を選定することが重要です。- 材料:切削工具には、硬度の高い材料を使用することが推奨されます。特に、コバルト合金、超硬合金(カーバイド)、またはチタン合金などの耐摩耗性が高い材料を選ぶと良いでしょう。
- コーティング:切削工具には、酸化アルミニウムやTiN(チタン窒化物)などのコーティングを施すことで、工具の耐摩耗性を向上させることができます。
- 工具形状:切削中の材料の切り屑を効率よく排出できる形状を選定することが重要です。特に、切り屑が絡まりやすいので、広めのチップを選ぶと効果的です。
切削条件
- 切削速度:A5056合金は比較的加工がしやすいため、適度な切削速度で加工することが推奨されます。通常、200~400メートル/分の範囲での切削速度が良い結果を生むことが多いです。
- 送り速度:送り速度は、加工する部品の形状や工具の種類に合わせて調整します。送り速度を高く設定することで、加工効率を高めることができますが、切削工具への負担を考慮して適切に設定することが大切です。
- 切削深さ:A5056合金の切削においては、切削深さは軽めに設定し、複数回の加工を行う方が良い場合があります。特に、高速切削時には深さを抑えることが重要です。
切削における問題点と対策
1. 切削中の熱発生とその管理
A5056合金は熱伝導性が高いため、切削中に発生する熱が工具や部品に蓄積しやすいです。このため、以下の対策を講じる必要があります。- 冷却液の使用:切削中の温度上昇を抑えるため、切削液(冷却液)を十分に供給することが重要です。冷却液は、切削工具や材料の温度を低く保ち、工具の摩耗を減少させます。
- 切削速度の調整:過度な切削速度は熱を過剰に発生させるため、適切な切削速度を選定し、冷却をしっかりと行うことが大切です。
2. 切り屑の処理
A5056合金は粘着性が高く、切削時に工具に付着した切り屑が原因で加工不良を引き起こすことがあります。これに対処するための方法は次の通りです。- 工具の形状と設計:切り屑を効率よく排出できるような工具の形状(チップ形状)を選択することで、切り屑の詰まりや工具への付着を防止できます。
- 高速回転と適切な送り速度:高速回転と適切な送り速度を組み合わせることで、切り屑を小さく細かくし、排出を容易にします。
3. 切削工具の摩耗
切削時の摩耗を防ぐためには、適切な切削条件と工具の選定が重要です。- 工具のコーティング:耐摩耗性を高めるために、切削工具にコーティングを施すことが有効です。特にTiNやTiAlN(チタンアルミナイト)などの硬質コーティングが有効です。
- 定期的な工具交換:工具の摩耗が進行した場合は、定期的に工具を交換することで加工精度を保ちます。
アルミ合金の切削加工のポイント
アルミ合金はその軽さと加工性の良さから多くの産業で使用されていますが、切削加工を行う際にはいくつかの注意点があります。ここでは、切削速度、フィードレート、冷却剤の使用と管理、加工精度を保つための工夫について解説します。切削速度とフィードレート
切削速度とフィードレートは、アルミ合金の加工効率と品質に大きな影響を与える重要な要素です。- 切削速度:アルミ合金は比較的軟らかく切削しやすいため、高速での切削が可能です。通常、切削速度は100~300メートル/分の範囲で設定されますが、合金の種類や工具の特性によって調整が必要です。特に高切削速度を使用すると、切削効率が向上し、仕上がりも良くなります。
- フィードレート:フィードレートは工具が材料に進む速度であり、効率よく材料を除去するためには適切に設定することが必要です。アルミ合金の場合、通常の切削では中程度のフィードレート(0.1~0.3mm/rev)が推奨されますが、高速切削を行う場合はフィードレートを増加させることもあります。ただし、過度に速いフィードレートは仕上がりに影響を与えることがあるため、バランスを取ることが重要です。
冷却剤の使用と管理
アルミ合金は熱伝導性が高いため、切削中に発生する熱を効果的に管理することが重要です。冷却剤の使用は、工具と材料の温度を低く保つために不可欠です。- 冷却剤の選定:冷却剤には水溶性冷却剤と油性冷却剤がありますが、アルミ合金の切削には水溶性冷却剤が一般的に使用されます。水溶性冷却剤は高い冷却効果を提供し、切削中に発生する熱を効率よく排出します。
- 冷却剤の供給量:冷却剤の供給量を十分に確保することで、切削面の温度上昇を防ぎ、工具の寿命を延ばすことができます。また、冷却剤が不足しないように定期的に補充し、冷却効果を最大限に活用します。
- 冷却剤の管理:冷却剤は切削中に汚れや油分が溜まることがあるため、定期的な清掃とフィルター交換が求められます。冷却剤の品質を維持することで、切削精度を保ち、工具の摩耗を最小限に抑えます。
加工精度を保つための工夫
アルミ合金の切削では、高い加工精度を保つためにいくつかの工夫が必要です。- 適切な工具選定:アルミ合金の切削においては、工具の材質や形状が重要です。特に、硬質合金やチタンコーティングされた工具は、アルミ合金の切削において優れた耐摩耗性を提供します。また、工具の形状や切削エッジも精度に影響を与えるため、専用の工具を使用することが推奨されます。
- 切削条件の最適化:切削速度やフィードレート、切削深さの調整は、加工精度に直結します。これらの条件は材料に適した範囲で設定し、過度な切削を避けることが大切です。試作を行い、最適な切削条件を見つけることが重要です。
- 工具の定期的な点検と交換:工具の摩耗が進行すると、加工精度が低下します。切削中に工具の摩耗具合を定期的にチェックし、必要に応じて交換することが、精度を保つためには必要です。
- 振動と引きずりの防止:切削中に発生する振動や引きずり(工具が材料に引っかかる現象)は、仕上がりに影響を与える可能性があります。これを防ぐためには、工具の選定や機械の安定性、切削条件を慎重に調整することが必要です。
アルミ合金の材質選定のポイント
アルミ合金の選定は、使用目的や環境に応じて、強度、加工性、耐食性、耐熱性などの特性を考慮することが重要です。ここでは、強度と加工性のバランス、合金の耐食性と耐熱性、用途に応じた合金の選び方について説明します。強度と加工性のバランス
アルミ合金は、強度と加工性のバランスを取ることが非常に重要です。強度が高いほど、材料が硬くなり、加工性が低下する傾向があります。以下の点を考慮して選定します。- 強度:アルミ合金は、一般的に軽量であり、鋼などの他の金属に比べて強度は低めですが、合金成分によって強度を高めることができます。強度が高い合金(例:7075)は構造材や航空機部品などに使用されますが、加工性が低くなる可能性があります。
- 加工性:加工性を重視する場合、強度よりも加工性を優先することが多くなります。例えば、1050や3003のような低強度で良好な加工性を持つ合金は、日常的な製品や装飾品に使用されます。
合金の耐食性と耐熱性
アルミ合金の選定において、耐食性と耐熱性も重要な要素です。使用する環境に応じて、合金の耐食性や耐熱性を考慮する必要があります。- 耐食性:アルミは酸化により耐食性が向上しますが、塩水や高湿度環境などでは腐食の問題が発生する可能性があります。海洋環境や化学薬品が多く使われる場所では、耐食性が高い合金(例:5052、5083)が推奨されます。これらの合金は、海洋構造物や化学プラントで広く使用されています。
- 耐熱性:アルミ合金は高温環境に弱いという特性がありますが、特定の合金は耐熱性を高めるために合金成分が調整されています。例えば、7075などの合金は比較的高い耐熱性を持ちますが、5000番台や6000番台は耐熱性に限界があります。高温で使用される部品には、耐熱性が強化された合金(例:2011、7050)が適しています。
用途に応じた合金の選び方
アルミ合金は、用途によって最適な合金が異なります。以下のような要素を考慮して選定します。- 構造部材や強度が求められる用途:高い強度が必要な構造部材や航空機部品などには、7075や7050などの高強度アルミ合金が適しています。これらは、軽量化と高強度を兼ね備えており、耐食性も良好です。
- 加工性を重視する用途:加工性が重視される場合、1050や3003のような低合金のアルミが最適です。これらの合金は、日常的な製品や家庭用品などで広く使われています。
- 耐食性が重要な用途:海洋環境や化学環境で使用される部品には、5052や5083などの耐食性が高い合金が選ばれます。これらは、塩水や化学薬品に強く、長期間にわたって腐食に耐えることができます。
- 熱的性能が求められる用途:高温環境に耐える部品には、耐熱性が強化されたアルミ合金(例:2011、7050など)が使用されます。これらは高温での性能維持に優れており、エンジン部品や航空機部品に利用されます。
アルミニウム合金の種類とその特徴
アルミニウム合金は、その成分や特性によりさまざまな種類に分類され、特定の用途に適した性能を発揮します。ここでは、一般的なアルミニウム合金の分類と各合金の特性・用途、さらにA5056合金の位置づけと利点について説明します。一般的なアルミニウム合金の分類
アルミニウム合金は主に以下のような分類がされます。これらは、主に合金元素の種類に基づいて分類されます。 1xxx 系(純アルミニウム)- 合金成分:99%以上の純度のアルミニウム。
- 特性:優れた耐食性、良好な加工性、導電性や熱伝導性が高い。
- 用途:電気機器、化学設備、食品・医薬品包装、建築材料など。
- 合金成分:銅(Cu)を主成分とし、強度が高い。
- 特性:高い強度と優れた耐熱性を持ち、耐食性はやや低い。
- 用途:航空機、宇宙産業、自動車、構造部材など。
- 合金成分:マンガン(Mn)を主成分とし、耐食性と加工性に優れた合金。
- 特性:良好な耐食性、適度な強度、優れた加工性を持つ。
- 用途:冷蔵庫、エアコン、熱交換器などの家庭用機器。
- 合金成分:マグネシウム(Mg)を主成分とし、非常に優れた耐食性を持つ。
- 特性:耐食性が高く、溶接性も良好。高い耐食性と良好な強度を備えており、特に海洋環境に適している。
- 用途:船舶、化学プラント、海洋設備など。
- 合金成分:シリコン(Si)とマグネシウム(Mg)を主成分とする合金。
- 特性:優れた加工性、良好な耐食性、適度な強度を持ちます。
- 用途:建築用部材、窓枠、家具、交通機器の構造部品など。
- 合金成分:亜鉛(Zn)を主成分とし、非常に高い強度を誇ります。
- 特性:強度が非常に高く、航空機部材や軍事用途に適しているが、耐食性は若干低い。
- 用途:航空機、宇宙産業、軍事用部品など。
各合金の特性と用途
各アルミニウム合金は、その特性に応じてさまざまな用途に使用されます。例えば:- 1xxx 系:非常に高い耐食性を持つため、化学プラントや電気機器の部品に使用されます。加工性も良いため、日常的な製品や装飾品に広く利用されます。
- 2xxx 系:高強度であり、耐熱性が必要な航空機や宇宙産業、また自動車の高強度部品にも使用されます。
- 3xxx 系:主に耐食性が要求される冷蔵庫や熱交換器、屋根材などの用途に使用されます。
- 5xxx 系:海洋環境で使用される船舶や海洋施設、化学設備など、特に耐食性が重視される分野で活躍します。
- 6xxx 系:適度な強度と耐食性を持ち、建築業界や輸送機器の部品として広く使用されています。
- 7xxx 系:高強度を誇り、航空機や軍事用途に利用されますが、耐食性が低いため、特別な処理が必要な場合もあります。
A5056合金の位置づけと利点
A5056は、5xxx 系に分類されるアルミニウム合金の一種です。この合金は、特に優れた耐食性を誇り、海洋環境や化学工業での使用に非常に適しています。- 位置づけ:A5056は、マグネシウムを主要合金元素としており、特に優れた耐食性と優れた加工性を持つため、化学プラントや海洋施設などで広く使用されています。その他にも、食品業界や家庭用機器にも利用されることがあります。
- 利点:
- 優れた耐食性:特に塩水環境での耐食性が高く、船舶や海洋機器に最適です。
- 良好な溶接性:溶接後も強度が維持されるため、複雑な構造物の製作にも適しています。
- 高い耐摩耗性:摩擦の多い環境でも耐久性が高く、長期間の使用が可能です。
高強度A5056合金の切削加工 – よくある質問とその解決策
A5056合金は、優れた耐食性と強度を持ち、さまざまな用途で使用される一方で、切削加工においては特有の問題が発生することがあります。ここでは、A5056合金の加工時に発生するよくある問題とその解決策、さらに長期的な加工品質を維持する方法について説明します。A5056合金の加工時のよくある問題
工具の摩耗と寿命- 問題:A5056合金は高強度を持つため、切削時に工具の摩耗が早く進行することがあります。特に硬い部分を加工する場合、工具の寿命が短くなることがあります。
- 解決策:
- 適切な工具の選定:硬質合金製の工具やコーティングツール(例えば、TiNコーティングやTiAlNコーティング)を使用することで、耐摩耗性を向上させ、工具寿命を延ばすことができます。
- 工具の冷却:適切な冷却剤を使用することで、工具の温度を下げ、摩耗を減少させます。
- 問題:A5056合金は、切削後の表面に微細な不規則な加工跡が残ることがあります。このような表面仕上げは、部品の性能に影響を与えることがあります。
- 解決策:
- 切削条件の調整:切削速度やフィードレートを最適化し、過剰な熱を発生させないようにします。また、加工の精度を保つために切削深さを適切に調整します。
- 表面仕上げの最適化:仕上げ加工を行うことで、加工後の表面の品質を改善できます。特に、最終仕上げの段階で適切な工具を使用し、余分なバリや不規則な跡を取り除きます。
- 問題:高強度A5056合金は、切削中に材料が変形することがあります。この変形は、加工精度に影響を与えるため、十分な対策が必要です。
- 解決策:
- 適切な支持とクランプ方法:部品をしっかりと固定するために、強力なクランプ装置を使用します。加えて、切削時の切削力を分散させるために複数の支持点を使用することが重要です。
- 切削力の分散:複数の段階に分けて切削を行うことで、過度な切削力が一度にかかるのを避けます。これにより、変形を最小限に抑えることができます。
切削加工の際のトラブルシューティング
オーバーヒート(工具の過熱)- 問題:A5056合金は高強度なため、切削中に熱が発生しやすいです。これが原因で、工具が過熱して摩耗が早く進むことがあります。
- 解決策:
- 冷却剤の使用:適切な冷却剤(例えば、ミスト冷却または高圧冷却)を使用し、切削中の温度を抑えることが必要です。
- 切削速度の見直し:切削速度を適切に調整して、熱の発生を最小限に抑えるようにします。過剰な速度は熱の発生を助長するため、バランスを取ることが重要です。
- 問題:切削中に材料がチッピング(欠け)することがあり、特に高速での切削や大きな切削深さで顕著に発生することがあります。
- 解決策:
- 切削条件の最適化:切削速度、フィードレート、切削深さを見直し、適切な範囲に設定します。また、切削中に材料が過剰に受ける圧力を減らすため、順番に浅く切削を行うことが有効です。
- 適切な切削工具の選定:鋭いエッジを持つ工具や適切なコーティングが施された工具を使用することで、チッピングを防ぐことができます。
- 問題:切削後、部品の端にバリが発生することが多く見られます。このバリが部品に付着したままでは、後続の工程や使用時に問題が発生する可能性があります。
- 解決策:
- 最適な切削条件の維持:切削速度、フィードレート、および工具の鋭さを維持し、バリの発生を最小限に抑えます。
- 後処理の実施:バリを取り除くために、手作業や機械でのバリ取りを行うことで、完成品の品質を保つことができます。
長期的な加工品質の維持方法
定期的な工具の交換とメンテナンス- 工具の摩耗を抑えるため、定期的な交換や研磨を行います。特に高強度材料での加工では、工具の状態を良好に保つことが加工品質の維持には欠かせません。
- 切削加工中は、温度や振動、切削力などを常に監視し、適切な調整を行います。これにより、加工中の不具合を未然に防ぎ、安定した品質を保つことができます。
- 加工後の部品の検査や測定を行い、規格に合った製品が作られていることを確認します。品質管理体制を整えることで、長期的に高い加工品質を維持できます。