「A7204合金の切削性を向上させるテクニックとは?」
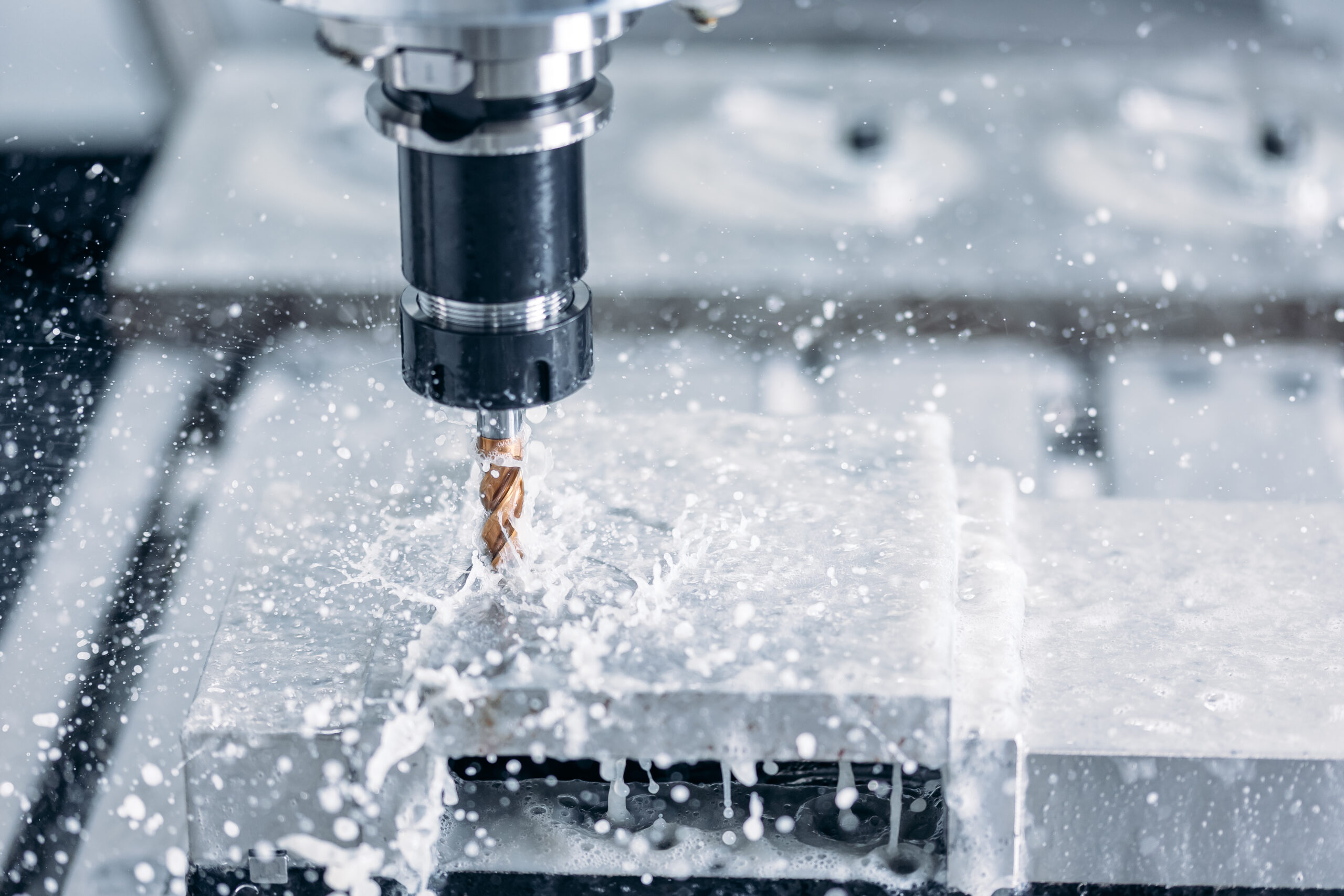
A7204合金は、その高い強度と耐食性で知られる優れた素材ですが、切削性に課題を抱えています。本記事では、A7204合金の切削性を向上させるためのテクニックについて探求していきます。切削性とは、工具が素材を切削する際の加工性能を指し、その向上は加工効率や品質向上に直結します。この貴重な合金の特性を最大限に活かすためには、どのようなアプローチが必要なのでしょうか?次の章で、A7204合金の切削性向上に向けた具体的な方法や革新的な手法について詳しく解説します。ご一読いただき、より効率的な加工技術の習得にお役立ていただければ幸いです。
目次
1. A7204合金とは
A7204合金は、アルミニウム合金の一種で、主に高い強度と耐食性を兼ね備えた材料です。航空機や自動車部品、その他の高性能機械部品に使用されることが多い合金で、厳しい条件下でも安定した性能を発揮します。1-1. A7204合金の特性
A7204合金は、優れた性能を有するアルミニウム合金で、以下の特性を持っています:- 1. 高強度
- 強度向上: A7204合金は高強度を特徴としており、アルミニウム合金の中でも比較的強度が高いです。これにより、重荷を支える構造材に最適です。
- 引張強度: 高い引張強度を有し、過酷な条件でも変形や破断が起きにくいです。
- 2. 優れた耐食性
- 耐腐食性: A7204合金は湿気や化学物質に強く、腐食や酸化の影響を受けにくいです。
- 塩水耐性: 特に海洋環境や湿気の多い場所で優れた耐腐食性を発揮します。
- 3. 良好な加工性
- 加工の容易さ: 高強度でありながらも加工がしやすいという特徴を持ち、切削加工や溶接が容易です。
- 鋳造性: 合金は鋳造性に優れており、複雑な形状を成形することができます。
- 4. 高温耐性
- 耐熱性: 高温環境においても安定した機械的性質を維持し、熱膨張が少ないため、温度変化に対する安定性があります。
- 耐熱強度: 高温下での強度低下が少ないため、エンジン部品などの高温環境での使用に適しています。
- 5. 軽量
- 低密度: A7204合金はアルミニウムを基にしているため、比重が軽く、強度対重量比が優れています。この特徴により、軽量化が要求される部品に広く使用されます。
- 6. 低膨張率
- 熱膨張: 合金は熱膨張率が低く、温度変化による形状の変化が少ないです。これにより、高精度な部品として使用されることが多いです。
- 7. 高い靭性
- 衝撃耐性: 靭性が高いため、衝撃や振動に対して耐性があり、耐衝撃性が求められる部品に最適です。
- 8. 良好な溶接性
- 溶接可能性: 他の高強度アルミニウム合金と比較して、溶接性も良好です。これにより、組み立てや製造プロセスの効率化が図れます。
- 9. 磁気特性
- 非磁性: A7204合金は非磁性のため、電子機器や精密機器での利用にも適しています。
- 10. 高い耐摩耗性
- 摩耗耐性: 高強度と耐食性を備えているため、摩耗しにくく、長寿命が求められる部品に最適です。
1-2. A7204合金の用途
A7204合金は、以下の用途に広く使用されています:- 航空機部品: 高強度と耐食性を活かして、航空機のフレームや翼などの構造部品に使用されます。
- 自動車産業: 軽量で強度が高いため、自動車のエンジン部品やシャーシにも使用されます。
- 機械部品: 高耐久性が要求される機械部品にも使用され、特に高温環境での性能が求められる場所に最適です。
1-3. A7204合金の組成と特徴
A7204合金は、アルミニウムを基にした合金で、主な成分として以下の元素を含みます:- アルミニウム (Al): 主成分。
- 銅 (Cu): 強度を高めるために含まれる。
- マグネシウム (Mg): 耐食性を向上させる。
- シリコン (Si): 合金の鋳造性を向上させる。
- 鉄 (Fe): 合金の強度を補強。
2. A7204合金の切削性の基礎
A7204合金は、その高強度と優れた耐食性により多くの産業分野で利用されていますが、切削加工においては特有の特性が存在します。以下に、A7204合金の切削性に関する基礎的な内容を詳述します。2-1. 切削性の定義と重要性
切削性とは、材料を加工する際に必要とされる力やエネルギー、また工具の摩耗の度合いなどを示す指標であり、材料が切削工具によってどれだけスムーズに切断できるかを表します。切削性が良い材料は、加工時間やエネルギーを削減でき、コスト効率が向上します。また、良好な切削性は工具の摩耗を抑え、工具寿命を延ばすと共に、加工精度を安定させるため、品質管理の面でも重要です。2-2. A7204合金の切削性の現状
A7204合金は高強度を特徴としており、その強度の高さが切削加工における課題の一つです。高強度の合金は、他の低強度のアルミニウム合金と比較して切削時に必要な力が大きく、切削速度や切削条件を適切に設定しないと、発熱や工具摩耗が激しくなることがあります。このため、切削時の温度上昇が問題となり、切削温度が高くなると部品の熱変形や工具の早期摩耗が引き起こされる可能性があります。 さらに、高強度材料に特有の切削困難さもあり、低速での切削や高精度が要求される場合には、特殊な工具や加工技術を使用する必要がある場合もあります。これらの要因が組み合わさることにより、A7204合金の切削性はやや難易度が高いものとなっています。2-3. 切削性に影響を与える要因
A7204合金の切削性に影響を与える要因にはいくつかの重要な要素があります。まず、材料の硬さが切削性に大きく影響します。A7204合金は硬度が高く、これにより切削工具の摩耗が速く進行することがあります。適切な工具選定が必要であり、耐摩耗性を持つ工具を使用することで、切削加工の効率が向上します。 また、切削中に発生する熱も切削性に大きな影響を与えます。高温で切削することで材料が軟化し、切削性が向上することがありますが、同時に熱膨張や材料の変形のリスクも高まります。このため、切削温度の管理が重要であり、適切な冷却材を使用することが求められます。 さらに、切削速度や送り速度も切削性に影響を与えます。切削速度が速すぎると工具の摩耗が進み、遅すぎると加工効率が低下します。このため、最適な切削条件を設定することが求められます。工具の材質も重要であり、A7204合金を切削する際には、高速鋼や超硬工具など、耐熱性や耐摩耗性に優れた工具を使用することが推奨されます。 最後に、加工時の切削力にも注意が必要です。A7204合金は高強度であるため、切削時の力が大きくなり、機械に負担がかかることがあります。安定した加工を行うためには、機械の剛性や切削条件の最適化が求められます。 これらの要因を考慮し、A7204合金の切削加工を効率的に行うためには、適切な工具選定や切削条件の調整、そして冷却方法の管理が不可欠です。3. A7204合金の切削性向上のためのテクニック
A7204合金の切削性を向上させるためには、いくつかのテクニックと対策が必要です。以下の要素に着目し、最適な切削結果を得るためのポイントを紹介します。3-1. 適切な切削工具の選択
A7204合金は高強度の合金であるため、切削工具の選択が非常に重要です。工具の素材や形状を慎重に選ぶことで、切削効率を向上させ、工具の寿命を延ばすことができます。具体的には、以下の工具が推奨されます。- 超硬工具: 高い耐摩耗性を持ち、A7204合金のような硬度の高い材料にも適しています。特に、強度が要求される精密な加工に有効です。
- コーティング工具: 高温に強いコーティング(例:TiN、TiAlNなど)を施した工具を選ぶことで、熱的負荷を軽減し、工具寿命を延ばすことができます。
3-2. 切削条件の最適化
A7204合金の切削において、切削条件(切削速度、送り速度、切削深さ)は加工効率や工具の摩耗に大きく影響します。以下の条件を最適化することで、切削性を向上させることができます。- 切削速度: 高すぎる切削速度は工具の摩耗を速めるため、適切な速度を選定することが重要です。合金の硬度に合わせた適正な切削速度を選び、加工品質と工具寿命のバランスを取ることが大切です。
- 送り速度: 適切な送り速度を設定することで、切削力を均等に分散させ、工具の摩耗を最小限に抑えることができます。また、送り速度が速すぎると、切り屑が適切に排出されず、熱の発生を助長する可能性があるため注意が必要です。
- 切削深さ: 適切な切削深さを設定することで、過度な負荷がかからず、安定した加工が可能になります。
3-3. 冷却剤の効果的な使用
冷却剤の使用は、切削性を向上させ、加工中の温度管理に重要な役割を果たします。A7204合金のような高強度材料は切削中に高温になるため、冷却が不十分だと工具の摩耗が加速し、切削効率が低下します。以下の点を考慮しましょう。- 冷却液の種類: 高温環境に適した冷却液(例えば、油性冷却液や高圧冷却液)を使用することで、摩擦を低減し、工具の温度上昇を防ぎます。
- 冷却方法: 切削面や工具に冷却液を直接噴射することで、熱を効率よく逃がすことができます。特に、高速切削時や重切削時には冷却液の効果を最大限に活用することが求められます。
3-4. 切削速度と送り速度の調整
切削速度と送り速度は、加工効率と仕上がり品質に大きく影響します。適切な速度を選ぶことで、以下のメリットを得ることができます。- 切削力の安定化: 高すぎる切削速度や送り速度は切削力を不安定にし、工具の摩耗を早めます。逆に、適切な速度を設定することで、切削力が均等になり、加工が安定します。
- 加工品質の向上: 適正な速度での切削により、加工表面の仕上がりが良好になります。また、切り屑の排出がスムーズになり、加工中の詰まりや熱の蓄積が防げます。
3-5. 工具のメンテナンスと交換時期
A7204合金を切削する際、工具の摩耗が進むと切削性が低下し、加工精度が悪化します。定期的なメンテナンスと適切なタイミングでの工具交換が不可欠です。- 工具のチェック: 切削前後に工具の状態を点検し、摩耗や欠けが見られる場合は、早めに交換することが重要です。摩耗が進むと、切削力が増し、仕上がりが悪化する可能性があります。
- 工具交換のタイミング: 高負荷な切削を行った後や、加工精度が低下した場合は、工具を交換することが推奨されます。交換時期を早期に把握することで、品質の安定性を確保できます。
4. 切削工具の種類と特性
切削工具は材料の加工を行うための重要な要素であり、材質、形状、コーティング技術によってその性能が大きく異なります。ここでは、切削工具の材質、形状、コーティング技術について詳しく説明し、それぞれがどのように工具の特性に影響を与えるかを見ていきます。4-1. 切削工具の材質と特徴
切削工具の材質は、主にその耐摩耗性、耐熱性、靭性に影響を与え、加工材料に適した工具選定を行う上で重要な要素です。代表的な材質とその特徴は以下の通りです。- 超硬合金(カルバイド):
- 特徴: 高い耐摩耗性と耐熱性を持つため、硬い金属や高温環境下での切削に適しています。加工速度が速く、工具寿命も長いです。
- 用途: 鋼、ステンレス、アルミニウムなどの切削に広く使用されます。
- 高速鋼(HSS):
- 特徴: 高温に強く、鋼や軽金属の切削に優れた性能を発揮します。価格が比較的安価であるため、一般的な切削に使われます。
- 用途: 軽金属、木材、プラスチックなどの切削に適しています。
- セラミック:
- 特徴: 非常に硬い材料で、耐熱性に優れ、高温下でも高い硬度を保ちます。ただし、脆い性質があるため衝撃には弱いです。
- 用途: 高硬度材料(例: 鋼、焼結金属)の加工に使用されます。
- CBN(立方晶窒化ホウ素):
- 特徴: 非常に硬い素材で、鋼などの高硬度材料の加工に特化しています。高温でも安定した性能を維持します。
- 用途: 高速切削や高精度加工に使用されます。
- ダイヤモンド:
- 特徴: 最も硬い素材で、摩耗や熱に強く、精密加工に適していますが、価格が非常に高いため特定の用途に限られます。
- 用途: 精密加工や切削が難しい材料(例: 繊維強化プラスチックや硬質材料)の切削に使用されます。
4-2. 工具形状の影響
切削工具の形状は、加工精度や切削性能に大きく影響を与えます。主な工具形状とその影響は次の通りです。- 切削刃の角度(主切刃角、背面角、前面角など):
- 影響: 刃の角度が適切でないと切削効率が悪化し、工具の摩耗が早くなります。例えば、前面角が小さいと切削抵抗が大きくなり、摩耗が進行しやすいです。
- 刃先の形状:
- 影響: 刃先がシャープであれば切削がスムーズに進み、仕上がりが良好になります。一方、丸みを帯びた刃先は強度が高くなるものの、切削効率が低下することがあります。
- 工具の長さと太さ:
- 影響: 長い工具は振動が発生しやすく、加工精度に影響を及ぼすことがあります。太い工具は剛性が高いですが、取り回しが難しくなることがあります。
- 切削工具の種類(ドリル、エンドミル、タップなど):
- 影響: 使用する加工方法によって最適な工具形状が異なります。例えば、ドリルは穴あけに最適であり、エンドミルはフライス加工に最適です。
4-3. コーティング技術と性能向上
切削工具に施すコーティングは、その耐摩耗性、耐熱性、化学的安定性を高め、工具寿命を延ばし、切削効率を向上させる役割を果たします。主なコーティング技術とその効果は次の通りです。- TiN(チタン窒化物):
- 特徴: 高い耐摩耗性と耐熱性を持ち、工具寿命を大幅に延ばします。また、摩擦係数が低いため、切削効率が向上します。
- 用途: 一般的な鋼材やアルミニウムの切削に広く使用されています。
- TiAlN(チタンアルミニウム窒化物):
- 特徴: TiNよりも高い耐熱性を持ち、過酷な切削条件でも安定した性能を発揮します。高温での切削に特化しています。
- 用途: ステンレス鋼、チタン合金、難削材の加工に適しています。
- AlCrN(アルミニウムクロム窒化物):
- 特徴: 高温でも優れた耐摩耗性を提供し、特に金属の加工において高い効果を発揮します。酸化しにくく、長寿命です。
- 用途: 高速切削、高温切削を必要とする工程に使用されます。
- Diamond Coating(ダイヤモンドコーティング):
- 特徴: ダイヤモンドコーティングは最も硬い素材であり、非常に高い耐摩耗性と低摩擦を実現します。硬質材の加工に最適です。
- 用途: セラミック、硬質金属、複合材料の加工に使用されます。
5. 切削パラメータの重要性
切削パラメータは、加工効率、工具寿命、仕上がり品質などに大きな影響を与えます。これらのパラメータを適切に設定することで、最適な切削を実現し、コスト削減や加工精度の向上が可能になります。ここでは、主な切削パラメータである「切削速度」「送り速度」「切削深さ」の影響について詳しく説明します。5-1. 切削速度の影響
切削速度は、工具が材料を切削する際の速度であり、切削の効率や工具寿命に大きな影響を与えます。切削速度は、通常、工具の回転数や材料の進行方向に関連しており、以下のような影響があります。- 高い切削速度:
- メリット: 高速で切削を行うことで加工時間が短縮され、生産性が向上します。また、摩擦熱が少なくなるため、加工面の仕上がりが向上することがあります。
- デメリット: ただし、切削速度が高すぎると、工具の摩耗が早く進み、工具寿命が短くなります。また、過剰な熱が発生し、材料が変形したり、工具が損傷したりする可能性があります。
- 低い切削速度:
- メリット: 切削温度が低く保たれ、工具の寿命が延びる可能性があります。また、精密な仕上がりが求められる場合に有利です。
- デメリット: 加工速度が遅くなり、生産性が低下することがあります。また、切削時間が長くなるため、効率的な加工が難しくなることもあります。
5-2. 送り速度の調整の重要性
送り速度は、工具が材料に対して進行する速度を示し、切削面の仕上がりや加工の安定性に影響を与えます。送り速度が適切に調整されていないと、以下のような問題が発生することがあります。- 高い送り速度:
- メリット: 加工時間を短縮でき、生産性が向上します。また、切削力が均等に分散されるため、工具の摩耗が均等になります。
- デメリット: 高すぎる送り速度は、加工面が粗くなり、仕上がりが悪化することがあります。また、工具に過度の負荷がかかり、工具寿命が短くなることもあります。
- 低い送り速度:
- メリット: 加工面が滑らかになり、精密な仕上がりが得られます。また、切削力が小さく、工具に対する負荷が軽減されることがあります。
- デメリット: 送り速度が低すぎると、加工時間が長くなり、効率が悪くなります。また、切削面における焼けや熱変形が発生する可能性があります。
5-3. 切削深さとその影響
切削深さは、1回の切削で材料が削られる深さを示し、加工精度や工具寿命に直結する要素です。切削深さが大きすぎると、次のような影響があります。- 大きな切削深さ:
- メリット: 一度に多くの材料を削ることができ、加工時間の短縮が可能です。特に荒削りの工程では、効率的な切削が求められます。
- デメリット: 切削深さが大きすぎると、工具にかかる負荷が大きくなり、工具が早く摩耗する可能性があります。また、切削中に材料の変形や焼けが発生しやすくなるため、仕上がりが悪化することがあります。
- 小さな切削深さ:
- メリット: 工具への負荷が小さく、工具寿命が延びる可能性があります。また、切削温度が低く抑えられるため、材料の変形が少なく、仕上がりが良好になります。
- デメリット: 切削深さが小さすぎると、加工時間が長くなり、効率的な加工が難しくなります。特に荒削りでの作業が非効率になることがあります。